Bearing ring small box detection system
A bearing ring and detection system technology, applied in sorting and other directions, can solve problems such as isolation of products that cannot be tested and untested products, inspection of non-conforming products, rework, and inability to perform traceability isolation, to ensure the detection cycle and automation. High-level, stable beat detection effect
- Summary
- Abstract
- Description
- Claims
- Application Information
AI Technical Summary
Problems solved by technology
Method used
Image
Examples
Embodiment Construction
[0028] Such as Figure 1 to Figure 4 ,as well as Figure 6 As shown, a small box detection system for bearing rings includes a frame 1, a feeding mechanism 2, a material tray 3, an entire column pushing mechanism 4, a qualified product pushing mechanism 5, a discharging mechanism 6 and a control mechanism 7, The top of the frame 1 is provided with a material storage platform 11, the material tray 3 is arranged on the middle part of the material storage platform 11, the feeding mechanism 2 and the unloading mechanism 6 are arranged on the left and right sides of the material tray 3, and the whole row of pushing mechanism 4 and Qualified product pushing mechanism 5 is arranged on the front and rear sides of the tray 3, and the tray 3 is provided with a plurality of alignment grooves 31 for placing bearing rings and two baffle plates 32 arranged at both ends of the alignment groove 31. The first row of grooves 31 parallel to each other; feeding mechanism 2 and the first row of g...
PUM
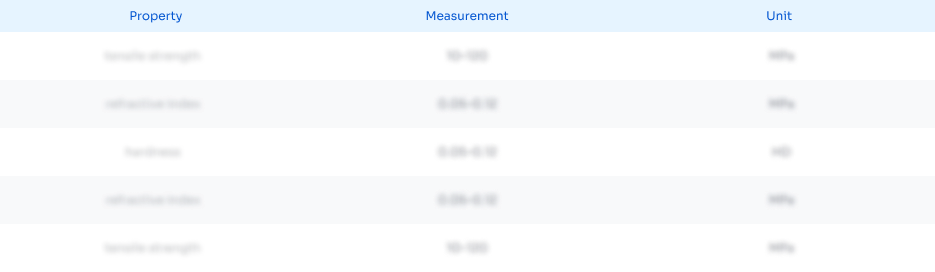
Abstract
Description
Claims
Application Information

- R&D Engineer
- R&D Manager
- IP Professional
- Industry Leading Data Capabilities
- Powerful AI technology
- Patent DNA Extraction
Browse by: Latest US Patents, China's latest patents, Technical Efficacy Thesaurus, Application Domain, Technology Topic, Popular Technical Reports.
© 2024 PatSnap. All rights reserved.Legal|Privacy policy|Modern Slavery Act Transparency Statement|Sitemap|About US| Contact US: help@patsnap.com