A detection method for the shape of pipe fittings based on three installation points
A shape detection and installation point technology, applied in the direction of measuring devices, instruments, etc., can solve the problems of not truly reflecting the installation angle deviation of pipe fittings and the gap between seams, so as to improve quality reliability and credibility, reduce production costs, reduce The effect of misjudgment
- Summary
- Abstract
- Description
- Claims
- Application Information
AI Technical Summary
Problems solved by technology
Method used
Image
Examples
Embodiment 1
[0050] A pipe fitting shape detection method based on three installation points includes a positioning method based on three installation points, a deviation calculation method and detection requirements. The positioning method based on three installation points includes three installation points and a spatial positioning method. The three installation points refer to three points closely related to the installation position: the two end points PE of the pipe fitting, and the bending tangent point PTmax of the maximum Lmax connecting the two end points PE. The spatial positioning method includes three steps: the first step is to determine the spatial triangle S from the three installation points of the theoretical pipe fitting, and the center of gravity G of the triangle S is determined; the second step is to use the same three installation points of the measured pipe fitting Determine the spatial triangle S1, and determine the center of gravity G1 of the triangle S; the third ...
Embodiment 2
[0055] On the basis of Example 1, for a certain 90° bending pipe, the straight sections at both ends are 100mm and 50mm respectively, and the spatial coordinates of the points on the center line of the theoretical pipe are T1 (0,100,0), T2 (150,100,0), T3 (200,50,0), T4 (200,0,0), the installation requires an angular deviation of ±3°, and the installation axial clearance is 0.5mm. When measuring the pipe to be tested, the accuracy of the measuring equipment should be at least 0.5 / 3=0.167mm. The actual laser vector measuring equipment has an accuracy of 0.001mm, which can be used to measure pipes. The actual measurement coordinates of the points on the center line of the tested pipe are P1 (0.800,59.600,125.000), P2 (90.061,14.970,125.000), P3 (112.021, -52.889,125.000), P4 (88.650, -97.65,125.000) ).
[0056] Calculation process: Use computer to calculate, the calculation accuracy is at least 0.5 / 100=0.005mm, the actual choice is 0.001mm. The straight line distance between T2 p...
PUM
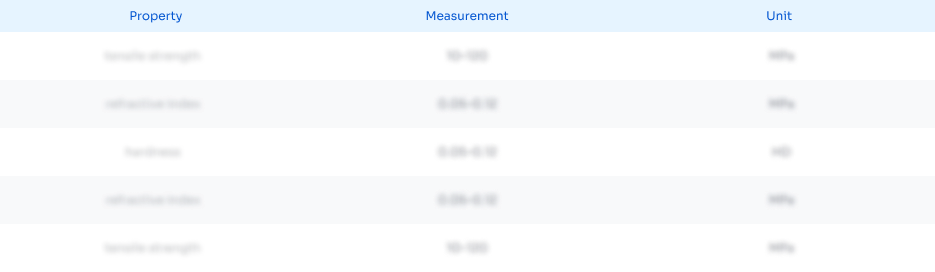
Abstract
Description
Claims
Application Information

- R&D
- Intellectual Property
- Life Sciences
- Materials
- Tech Scout
- Unparalleled Data Quality
- Higher Quality Content
- 60% Fewer Hallucinations
Browse by: Latest US Patents, China's latest patents, Technical Efficacy Thesaurus, Application Domain, Technology Topic, Popular Technical Reports.
© 2025 PatSnap. All rights reserved.Legal|Privacy policy|Modern Slavery Act Transparency Statement|Sitemap|About US| Contact US: help@patsnap.com