A typical damage repair process of engine reverse thrust grille
A damage repair and engine technology, applied in the field of aircraft maintenance, to achieve the effect of expanding the scope of repair, clearing technical blind spots, and reducing maintenance costs
- Summary
- Abstract
- Description
- Claims
- Application Information
AI Technical Summary
Problems solved by technology
Method used
Image
Examples
Embodiment 1
[0042] A typical damage repair process for an engine reverse thrust grille, comprising the following steps:
[0043] 1) Determine the typical damage types of the engine thrust reverser grille, including hyperboloid edge aperture damage and metal guide vane damage;
[0044] 2) For hyperboloid edge aperture damage, the repair methods include:
[0045] 2.1 The shape of the grid is kept in the grid near the hyperbolic edge aperture damage area. Set a separation film (not shown in the figure), and set a filler 1 (filler part number) in the separation film (part number of the separation film QZ5111). EC3524 B / A), such as figure 2 shown;
[0046] 2.2 Repair of the outer surface of the grid For the hyperboloid edge aperture damage area 2 Repair from the outer surface, such as image 3 As shown, the slope is firstly polished, and after the grinding is completed, the carbon fiber prepreg 3 is laid layer by layer from the outer surface of the hole damage area to the slope to form a f...
Embodiment 2
[0057] A typical damage repair process for an engine reverse thrust grille, comprising the following steps:
[0058] 1) Determine the typical damage types of the engine thrust reverser grille, including hyperboloid edge aperture damage and metal guide vane damage;
[0059] 2) For hyperboloid edge aperture damage, the repair methods include:
[0060] 2.1 The shape of the grid is kept in the grid near the hyperbolic edge aperture damage area, and the blue high-temperature separation tape is set in the grid, and the filling glue is set in the tape, such as figure 2 shown;
[0061] The blue tape is AIRIECH:Flashbreaker 1R, and the filling glue is EC3524 B / A.
[0062] The method of using blue tape and structural filling glue can ensure the strength of the filling structure and effectively prevent secondary damage to the original structure.
[0063] 2.2 The repair of the outer surface of the grille is repaired from the outer surface of the hyperboloid edge aperture damage area, ...
Embodiment 3
[0077] A typical damage repair process for an engine reverse thrust grille, comprising the following steps:
[0078] 1) It is determined that the typical damage type of the engine reverse thrust grid is the hyperboloid edge aperture damage;
[0079] 2) For hyperboloid edge aperture damage, the repair methods include:
[0080] 2.1 The shape of the grid is kept in the grid near the hyperbolic edge aperture damage area, and the blue high-temperature separation tape is set in the grid, and the filling glue is set in the tape, such as figure 2 shown;
[0081] The blue tape is AIRIECH:Flashbreaker 1R, and the filling glue is EC3524 B / A.
[0082] The method of using blue tape and structural filling glue can ensure the strength of the filling structure and effectively prevent secondary damage to the original structure.
[0083] 2.2 The repair of the outer surface of the grille is repaired from the outer surface of the hyperboloid edge aperture damage area, such as image 3 As sho...
PUM
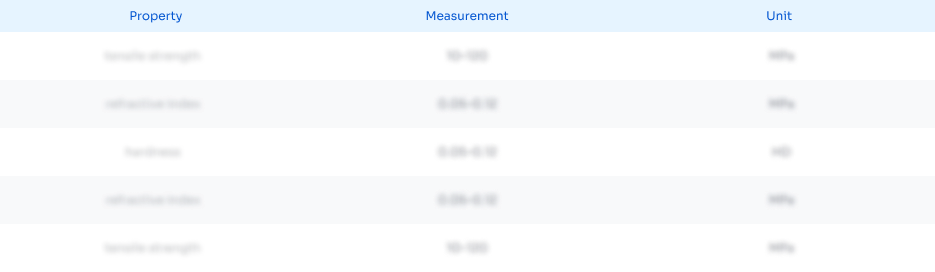
Abstract
Description
Claims
Application Information

- R&D
- Intellectual Property
- Life Sciences
- Materials
- Tech Scout
- Unparalleled Data Quality
- Higher Quality Content
- 60% Fewer Hallucinations
Browse by: Latest US Patents, China's latest patents, Technical Efficacy Thesaurus, Application Domain, Technology Topic, Popular Technical Reports.
© 2025 PatSnap. All rights reserved.Legal|Privacy policy|Modern Slavery Act Transparency Statement|Sitemap|About US| Contact US: help@patsnap.com