Processing center coordinate system setting method
A machining center and coordinate system technology, applied in general control systems, control/adjustment systems, instruments, etc., can solve the problems of increasing the difficulty of debugging and low efficiency, and achieve the effects of intuitive and clear dimensional relationships, improved efficiency, and simplified times.
- Summary
- Abstract
- Description
- Claims
- Application Information
AI Technical Summary
Problems solved by technology
Method used
Image
Examples
Embodiment
[0013] Example: such as figure 1 As shown, in the process of processing an aluminum product, the method of setting the coordinate system of the machining center is introduced. The same coordinate system is used for 5-face machining, which coincides with the marking datum, and the size relationship is intuitive and clear. At the same time, it simplifies the number of times to set the coordinate system and improves work efficiency. Since the dimensions of each processing surface are interrelated, there is no need to consider the impact on other processing surfaces when modifying the coordinate system, which reduces the workload of debugging engineers and technicians.
[0014] In the process of making the program, a macro program is introduced to set the tool length, radius value, coordinate system and other related processing parameters through the macro program. Taking the OKUMA OSP-P200-R system machine tool for debugging aluminum products in our company as an example,
[001...
specific example
[0019] Specific examples (partial procedures) are as follows
[0020]
[0021] After the processing program is debugged by engineers and technicians, set the relevant coordinate system, tool length, radius and other parameters in the program, and then close the program editing function through the key button on the machine panel. At this time, the processing program and The correctness of processing parameters. Completely avoid errors caused by human factors.
PUM
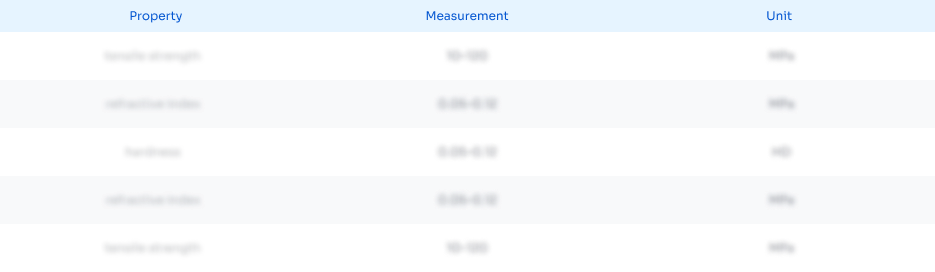
Abstract
Description
Claims
Application Information

- R&D Engineer
- R&D Manager
- IP Professional
- Industry Leading Data Capabilities
- Powerful AI technology
- Patent DNA Extraction
Browse by: Latest US Patents, China's latest patents, Technical Efficacy Thesaurus, Application Domain, Technology Topic, Popular Technical Reports.
© 2024 PatSnap. All rights reserved.Legal|Privacy policy|Modern Slavery Act Transparency Statement|Sitemap|About US| Contact US: help@patsnap.com