An Adaptive Pipeline Dredging Robot
A robotic and self-adaptive technology, applied in the field of robotics science, which can solve the problems of pipeline accidents, losses, difficulty in detection and cleaning, etc.
- Summary
- Abstract
- Description
- Claims
- Application Information
AI Technical Summary
Problems solved by technology
Method used
Image
Examples
Embodiment Construction
[0027] The principles and features of the present invention are described below in conjunction with the accompanying drawings, and the examples given are only used to explain the present invention, and are not intended to limit the scope of the present invention.
[0028] Such as figure 1 , figure 2 , image 3 , Figure 4 , Figure 5 , Figure 6 , Figure 7 As shown, an adaptive pipeline dredging robot includes a shell 1, a reamer dredging mechanism 2, a camera 3 and a plurality of walking devices 4, the reamer dredging mechanism 2 is arranged at the front end of the shell 1, and the camera 3 is set On the housing 1, the camera 3 is preferably arranged at the front end of the housing 1, and the number of the running gear 4 is preferably three, wherein the running gear 4 includes a diameter-changing mechanism, a running gear 430 and a pressure-sensing module 440. The diameter mechanism is arranged on the casing 1 , the traveling mechanism 430 is arranged at the output en...
PUM
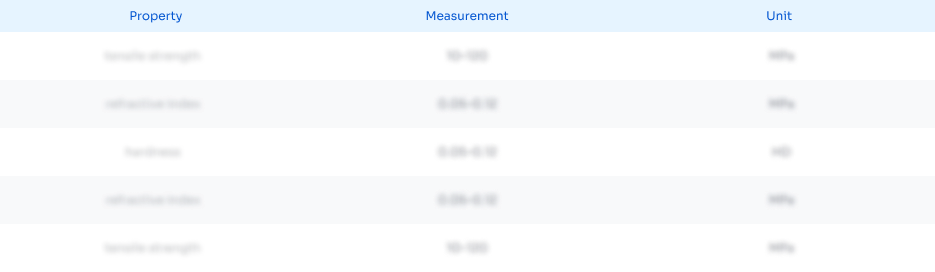
Abstract
Description
Claims
Application Information

- R&D
- Intellectual Property
- Life Sciences
- Materials
- Tech Scout
- Unparalleled Data Quality
- Higher Quality Content
- 60% Fewer Hallucinations
Browse by: Latest US Patents, China's latest patents, Technical Efficacy Thesaurus, Application Domain, Technology Topic, Popular Technical Reports.
© 2025 PatSnap. All rights reserved.Legal|Privacy policy|Modern Slavery Act Transparency Statement|Sitemap|About US| Contact US: help@patsnap.com