Pipe measuring and straightening integrated machine
An all-in-one machine and pipe fitting technology, applied in the field of pipe fitting measurement and straightening all-in-one machine, can solve problems such as bending, low concentricity, and straightening accuracy cannot be further guaranteed
- Summary
- Abstract
- Description
- Claims
- Application Information
AI Technical Summary
Problems solved by technology
Method used
Image
Examples
Embodiment Construction
[0024] The following is attached figure 1 ~ attached image 3 The present invention is described in further detail.
[0025] An all-in-one machine for measuring and straightening pipe fittings, comprising a placement plane 1, which is set horizontally, and two support seats 2 are fixed on the placement plane 1, and each support seat 2 is provided with a set for simultaneously pressing against the top and waiting for straightening The tops 3 at the two ends of the pipe fittings include abutting screws 31. The two abutting screws 31 are on the same horizontal plane. When between the two support seats 2, the end of the jacking bolt 9 can be offset against the end of the pipe fitting to be straightened.
[0026] A measuring section 4 is arranged between the two supporting platforms. The measuring section 4 includes a horizontally arranged main connecting bar 5, a horizontally arranged secondary connecting bar 6, an adjustment ring 7, and a measuring ring 8. The number of the mai...
PUM
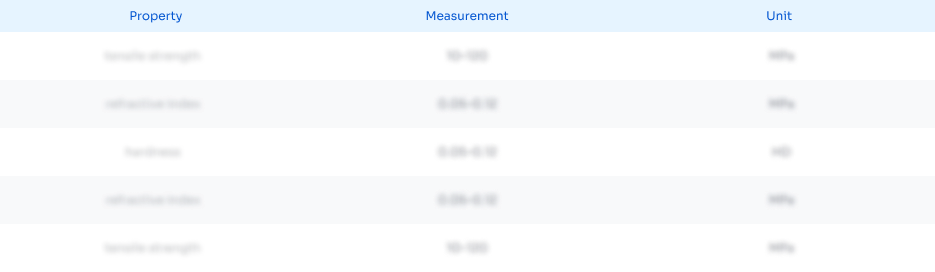
Abstract
Description
Claims
Application Information

- R&D
- Intellectual Property
- Life Sciences
- Materials
- Tech Scout
- Unparalleled Data Quality
- Higher Quality Content
- 60% Fewer Hallucinations
Browse by: Latest US Patents, China's latest patents, Technical Efficacy Thesaurus, Application Domain, Technology Topic, Popular Technical Reports.
© 2025 PatSnap. All rights reserved.Legal|Privacy policy|Modern Slavery Act Transparency Statement|Sitemap|About US| Contact US: help@patsnap.com