Remote real-time control method, based on demonstrative articulated arm, for industrial robot
A technology of industrial robots and articulated arms, applied in manipulators, manufacturing tools, program-controlled manipulators, etc., can solve problems such as personal safety and physical and mental health hazards of operators, achieve the effects of reducing skill level requirements, ensuring personal safety, and improving efficiency
- Summary
- Abstract
- Description
- Claims
- Application Information
AI Technical Summary
Problems solved by technology
Method used
Image
Examples
Embodiment Construction
[0011] refer to figure 1 , this embodiment is a remote real-time control method for an industrial robot based on the teaching joint arm. The operator learns the on-site operation situation through the visual feedback system, and the operator operates the teaching joint arm of the industrial robot according to the visual feedback system, and the teaching joint Each joint of the arm is equipped with an angle sensor, and each angle sensor is connected to the angle data acquisition module through SSI communication, and the angle data acquisition module is connected to the motion controller of the industrial robot through the K-BUS bus communication, and the angle data The acquisition module periodically collects the position information of the angle sensor through the SSI protocol and transmits it to the motion controller of the robot through the K-BUS bus; the industrial robot connected to the teaching joint arm communicates with the computer system through the OPC protocol throug...
PUM
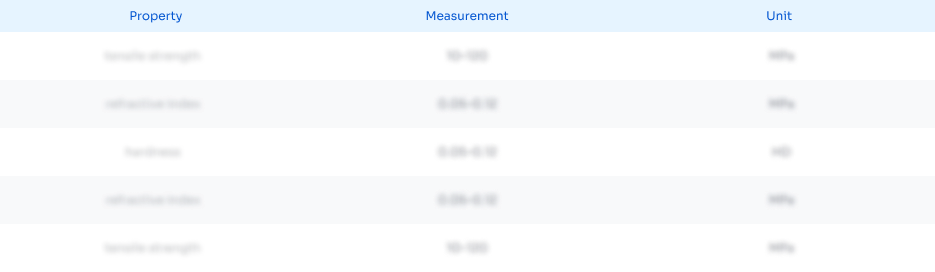
Abstract
Description
Claims
Application Information

- R&D
- Intellectual Property
- Life Sciences
- Materials
- Tech Scout
- Unparalleled Data Quality
- Higher Quality Content
- 60% Fewer Hallucinations
Browse by: Latest US Patents, China's latest patents, Technical Efficacy Thesaurus, Application Domain, Technology Topic, Popular Technical Reports.
© 2025 PatSnap. All rights reserved.Legal|Privacy policy|Modern Slavery Act Transparency Statement|Sitemap|About US| Contact US: help@patsnap.com