Tool device capable of controlling sheet welding gap
A thin plate welding and gap technology, applied in auxiliary devices, manufacturing tools, welding equipment, etc., can solve problems such as inability to clamp, achieve quality assurance, improve welding quality, and convenient gap control
- Summary
- Abstract
- Description
- Claims
- Application Information
AI Technical Summary
Problems solved by technology
Method used
Image
Examples
Embodiment Construction
[0020] Below according to the appendix Figures 1 to 4 , the preferred embodiments of the present invention are given and described in detail, so that the functions and characteristics of the present invention can be better understood.
[0021] see Figures 1 to 4 , a tooling device that can control the welding gap of a thin plate according to an embodiment of the present invention includes a fixed base 1, a plurality of quick indenters 2, two base plates 3, eight first bolts 4 and a plurality of second bolts (not shown in the figure). A groove 11 is formed in the middle of the fixed base 1, and the bottom of the groove 11 is evenly distributed along the extending direction of the groove 11 to form a plurality of gas injection holes 12; both sides of the groove 11 are formed along the extending direction of the groove 11. A plurality of first fastening screw holes 13; four first connecting screw holes 15 are respectively formed on both sides of the groove 11, and the first bo...
PUM
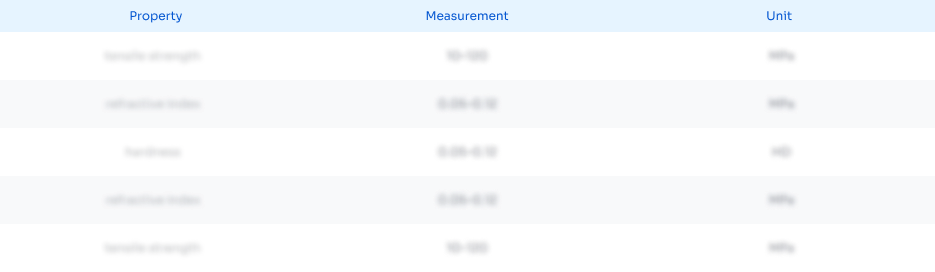
Abstract
Description
Claims
Application Information

- R&D
- Intellectual Property
- Life Sciences
- Materials
- Tech Scout
- Unparalleled Data Quality
- Higher Quality Content
- 60% Fewer Hallucinations
Browse by: Latest US Patents, China's latest patents, Technical Efficacy Thesaurus, Application Domain, Technology Topic, Popular Technical Reports.
© 2025 PatSnap. All rights reserved.Legal|Privacy policy|Modern Slavery Act Transparency Statement|Sitemap|About US| Contact US: help@patsnap.com