Comb type mixing nozzle of injection molding machine
An injection molding machine and comb-type technology, which is applied in the field of comb-type mixing nozzles, can solve the problems of lower assembly efficiency, assembly trouble, and cost increase, and achieve the effects of improved assembly efficiency, convenient maintenance, and reduced manufacturing costs
- Summary
- Abstract
- Description
- Claims
- Application Information
AI Technical Summary
Problems solved by technology
Method used
Image
Examples
no. 1 example
[0040] see Figure 1-Figure 21 The comb-shaped mixing nozzle of this injection molding machine includes a nozzle head 1 and a nozzle body 2 connected to each other. The inner cavity of the nozzle body 2 is provided with a comb-shaped mixing part 3. The comb-shaped mixing part 3 is a columnar body, and its surface There are two feed channels 3.1 and two discharge channels 3.4; one end of the feed channel 3.1 is closed and the other end is open, and it runs through to the feed end of the comb-shaped mixing part 3. The open end of the feed channel 3.1 is connected to the The inner cavity of the nozzle body 2 is directly connected; one end of the discharge channel 3.4 is closed and the other end is open, and it runs through to the discharge end of the comb-shaped mixing part 3, and the open end of the discharge channel 3.4 is directly connected to the inner cavity of the nozzle head 1 ; There is a glue comb structure between the feed channel 3.1 and the discharge channel 3.4, and ...
no. 2 example
[0048] see Figure 22-Figure 24 , the comb-shaped mixing nozzle of this injection molding machine is different from the first embodiment in that: the nozzle head 1 is a through structure, and its inner wall is provided with a second limiting boss 1.3, and the comb-shaped mixing part 3 is arranged on the nozzle head 1 The inner cavity, the second limiting boss 1.3 the discharge end of the comb-shaped mixing part 3; the outer wall of the nozzle head 1 is provided with the second external thread 1.4, the inner wall of the nozzle body 2 is provided with the second internal thread 2.4, the nozzle The body 2 and the nozzle head 1 are screwed to each other through the internal and external threads 2.3; the end of the nozzle head 1 is provided with a second connecting shaft 1.5, and the inner wall of the nozzle body 2 is provided with a second connection hole 2.5, when the nozzle body 2 and the nozzle head 1 are connected , the second connecting hole 2.5 and the second connecting shaf...
PUM
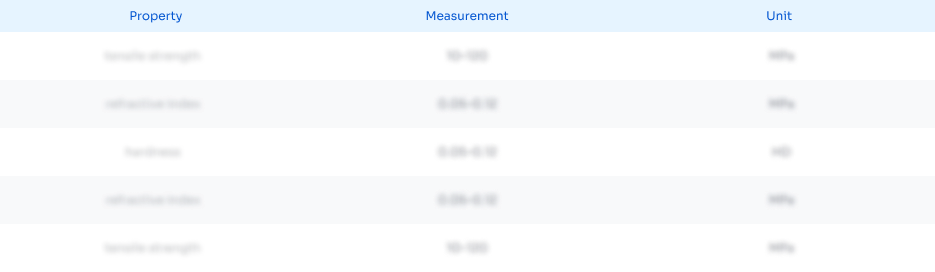
Abstract
Description
Claims
Application Information

- R&D Engineer
- R&D Manager
- IP Professional
- Industry Leading Data Capabilities
- Powerful AI technology
- Patent DNA Extraction
Browse by: Latest US Patents, China's latest patents, Technical Efficacy Thesaurus, Application Domain, Technology Topic, Popular Technical Reports.
© 2024 PatSnap. All rights reserved.Legal|Privacy policy|Modern Slavery Act Transparency Statement|Sitemap|About US| Contact US: help@patsnap.com