Self-controlled control textile winding mechanism
A winding mechanism and textile technology, applied in the direction of conveying filamentous materials, thin material processing, transportation and packaging, etc., can solve the problems of inconvenient use, low work efficiency, waste of man-hours, etc., to improve work efficiency and improve efficiency. , easy to use effect
- Summary
- Abstract
- Description
- Claims
- Application Information
AI Technical Summary
Problems solved by technology
Method used
Image
Examples
Embodiment Construction
[0022] Such as Figure 1-Figure 6 As shown, a self-selective control textile winding mechanism of the present invention includes a base 5 and winding mechanisms 6 equidistantly distributed on the top end surface of the base 5, and each of the bases 5 below the winding mechanism 6 There is a drive cavity 51 extending to the front side inside. The rear side of the drive cavity 51 is communicated with a first cavity 53 extending left and right. The base 5 on the front side of the first cavity 53 is provided with a The second cavity 54, a partition 55 is arranged between the first cavity 53 and the second cavity 54, and the inner top wall on the front side of each first cavity 53 is provided with a guide groove 52 Each of the sliding guide grooves 52 is provided with a sliding block 510 extending downward, and the bottom extension of the sliding block 510 extends into the driving cavity 51 and slidably fits with the inner bottom wall of the driving cavity 51 connected, each of th...
PUM
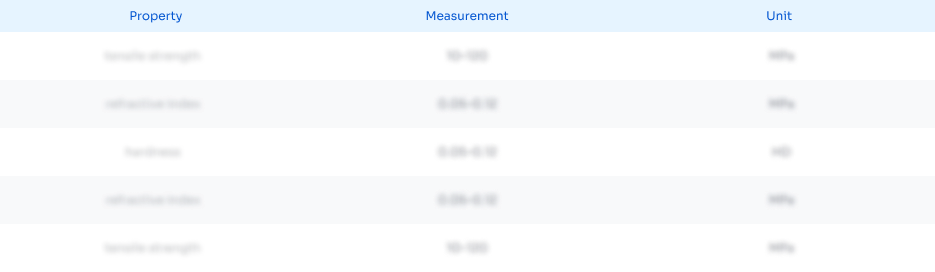
Abstract
Description
Claims
Application Information

- R&D
- Intellectual Property
- Life Sciences
- Materials
- Tech Scout
- Unparalleled Data Quality
- Higher Quality Content
- 60% Fewer Hallucinations
Browse by: Latest US Patents, China's latest patents, Technical Efficacy Thesaurus, Application Domain, Technology Topic, Popular Technical Reports.
© 2025 PatSnap. All rights reserved.Legal|Privacy policy|Modern Slavery Act Transparency Statement|Sitemap|About US| Contact US: help@patsnap.com