Self-learning method for dpf differential pressure sensor
A self-learning method and sensor technology, applied in the field of engines, can solve the problems of burning DPF, aging water vapor, pressure difference carbon load deviation, etc., and achieve the effects of improving measurement accuracy, improving safety, and reducing measurement deviation.
- Summary
- Abstract
- Description
- Claims
- Application Information
AI Technical Summary
Problems solved by technology
Method used
Image
Examples
Embodiment Construction
[0019] Exemplary embodiments of the present disclosure will be described in more detail below with reference to the accompanying drawings. Although exemplary embodiments of the present disclosure are shown in the drawings, it should be understood that the present disclosure may be embodied in various forms and should not be limited by the embodiments set forth herein. Rather, these embodiments are provided for more thorough understanding of the present disclosure and to fully convey the scope of the present disclosure to those skilled in the art.
[0020] figure 1 It is a flow chart of the self-learning method for the DPF differential pressure sensor described in the present invention. figure 2 Control logic diagram for self-learning of DPF differential pressure sensor. Such as figure 1 As shown, the self-learning method for the DPF differential pressure sensor described in the present invention is used to correct the measurement characteristic curve of the differential pr...
PUM
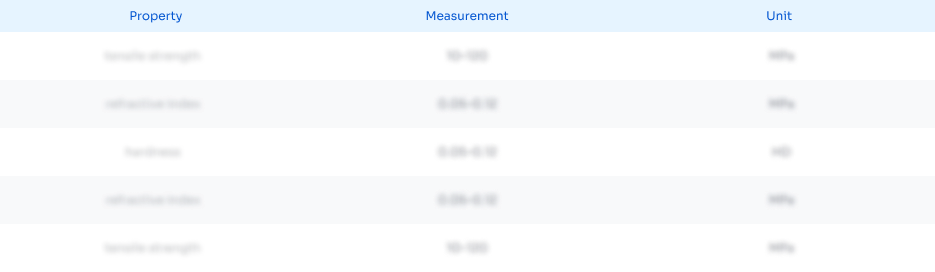
Abstract
Description
Claims
Application Information

- R&D
- Intellectual Property
- Life Sciences
- Materials
- Tech Scout
- Unparalleled Data Quality
- Higher Quality Content
- 60% Fewer Hallucinations
Browse by: Latest US Patents, China's latest patents, Technical Efficacy Thesaurus, Application Domain, Technology Topic, Popular Technical Reports.
© 2025 PatSnap. All rights reserved.Legal|Privacy policy|Modern Slavery Act Transparency Statement|Sitemap|About US| Contact US: help@patsnap.com