Double hook automatic hoisting structure and hoisting method
A hoisting and automatic technology, applied in the directions of traveling mechanism, transportation and packaging, load hoisting elements, etc., can solve the problems of large swing, inability to automatically hook the mold, and inability to realize automatic hoisting operations, to ensure safety and stability. Effect
- Summary
- Abstract
- Description
- Claims
- Application Information
AI Technical Summary
Problems solved by technology
Method used
Image
Examples
Embodiment 1
[0009] Embodiment 1: with reference to attached figure 1 . A double-hook automatic hoisting structure, including a PLC controller, is composed of a mobile crane frame 100, a left crane 101, and a right crane 102; the left crane 101 and the right crane 102 are installed on the mobile crane frame 100 Both ends and the left crane 101 and the right crane 102 are synchronously raised or lowered under the control of PLC. The left crane 101 is composed of a hook 115, a lift 104, a servo motor 103, a guide shaft 121, a sliding bearing 201, a detection switch 116, a servo motor 105, a reducer 106, a transmission gear 107, a rack 108, a guide rail 122, and a plate 200. . The rack 108 and two guide rails 122 are fixed on the crane frame 100, the plate 200 is fixed on the slide block of the guide rail 122, the reducer 106 is fixed on the plate 200 and the servo motor 105 is connected with the reducer 106, and the transmission gear 107 is fixed On the output shaft of the speed reducer 1...
Embodiment 2
[0010] Embodiment 2: On the basis of Embodiment 1, a hoisting method of a double-hook automatic hoisting structure, the left and right cranes 101 and 102 lift up and down, and the lifters 104 and 110 are driven by servo motors 103 and 109 to lift up and down the hooks 115 and 116 When lifting, it is guided by two or more guide shafts 121 and 124 to prevent the hook from swinging. When hoisting, the hooks 115 and 117 of the left crane 101 and the right crane 102 are equipped with two detection switches 116 and 118. , when the mold is lifted by hooks 115 and 117, 9 pairs of left boom 120 and right boom 119 are detected, and the lifting position is checked. If the position is inconsistent with the detection, the crane cannot lift; if the position is consistent with the detection , The lifting of the left crane 101 and the right crane 102 is controlled synchronously in position, so that the hoisted mold can be lifted and lowered smoothly. The left crane 101 is driven by the servo ...
PUM
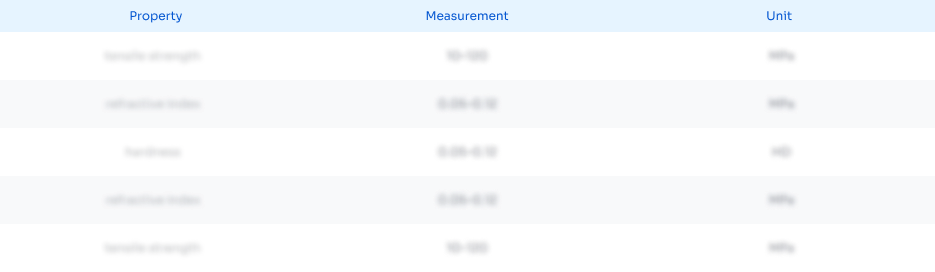
Abstract
Description
Claims
Application Information

- Generate Ideas
- Intellectual Property
- Life Sciences
- Materials
- Tech Scout
- Unparalleled Data Quality
- Higher Quality Content
- 60% Fewer Hallucinations
Browse by: Latest US Patents, China's latest patents, Technical Efficacy Thesaurus, Application Domain, Technology Topic, Popular Technical Reports.
© 2025 PatSnap. All rights reserved.Legal|Privacy policy|Modern Slavery Act Transparency Statement|Sitemap|About US| Contact US: help@patsnap.com