Temperature Compensation Method of Optical Fiber Pneumatic Measuring Balance
A temperature compensation and aerodynamic technology, which is applied in the field of aerospace force measurement test, can solve the problems of serious temperature effect and electromagnetic interference resistance, and achieve the effect of reducing heat output and significant compensation effect.
- Summary
- Abstract
- Description
- Claims
- Application Information
AI Technical Summary
Problems solved by technology
Method used
Image
Examples
Embodiment 1
[0067] In this embodiment, the optical fiber aerodynamic measurement balance structure adopts a commonly used rod-type three-component aerodynamic measurement balance structure, which is cylindrical in shape, including the model connection end 1, axial force element 3, normal force and pitch Moment combination elements 2 and 4, strut 5 and model support connection end 6, model connection end 1 is processed into a taper of 1:5 and connected with the test model, model support connection end 6 is processed into a cylindrical surface, connected with the model support, in two The axial force element 3, the combined elements 2 and 4 of the normal force and pitching moment are set between the ends, and placed inside the test model for measuring the aerodynamic force / moment of the model. The rear end of the measuring element is a strut, which is a straight cylindrical section. In order to meet the rigidity requirements, it is designed as a conical section at the connection with the mod...
PUM
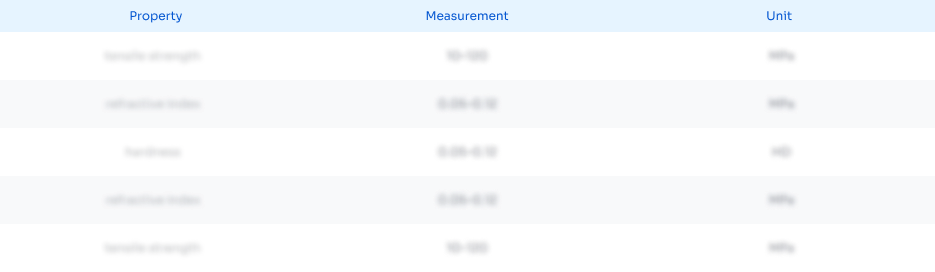
Abstract
Description
Claims
Application Information

- R&D Engineer
- R&D Manager
- IP Professional
- Industry Leading Data Capabilities
- Powerful AI technology
- Patent DNA Extraction
Browse by: Latest US Patents, China's latest patents, Technical Efficacy Thesaurus, Application Domain, Technology Topic, Popular Technical Reports.
© 2024 PatSnap. All rights reserved.Legal|Privacy policy|Modern Slavery Act Transparency Statement|Sitemap|About US| Contact US: help@patsnap.com