Sintering furnace for composite reinforcing material used for production of silicon aerogel thermal insulation felt
A composite reinforcement, silicon aerogel technology, applied in furnaces, furnace types, lighting and heating equipment, etc., can solve the problems of long sintering time, low strength of silicon aerogel, uneven thermal energy distribution, etc., to improve the sintering rate and Sintering effect, providing thermal energy utilization, increasing the effect of sintering area
- Summary
- Abstract
- Description
- Claims
- Application Information
AI Technical Summary
Problems solved by technology
Method used
Image
Examples
Embodiment Construction
[0025] In order to make the technical solution of the present invention clearer, the present invention will be further described below in conjunction with the accompanying drawings. Any solution obtained by equivalent replacement and conventional reasoning of the technical features of the technical solution of the present invention falls within the protection scope of the present invention.
[0026] As shown in the figure, a sintering furnace for composite reinforcing materials used in the production of silicon airgel insulation blankets includes a sintering furnace main body 11. Cylindrical furnace door 12;
[0027] The inner wall of the main body 11 of the sintering furnace and the inner wall of the furnace door 12 are semi-cylindrical, and fit each other to form a sintering chamber, and the sintering chamber is sequentially provided with a sintering bracket 1, a heating tube 13 and a graphite furnace from the inside to the outside. piece 14;
[0028] The quantity of descri...
PUM
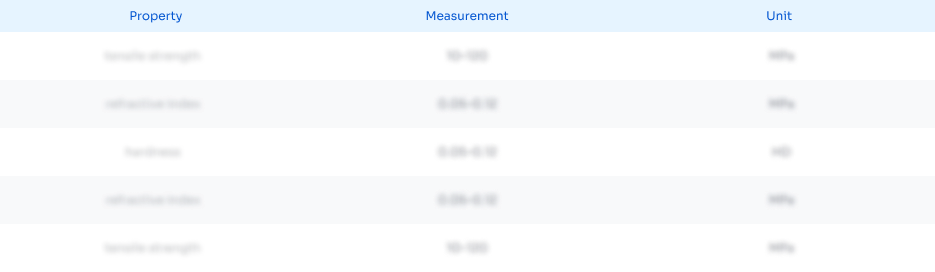
Abstract
Description
Claims
Application Information

- R&D Engineer
- R&D Manager
- IP Professional
- Industry Leading Data Capabilities
- Powerful AI technology
- Patent DNA Extraction
Browse by: Latest US Patents, China's latest patents, Technical Efficacy Thesaurus, Application Domain, Technology Topic, Popular Technical Reports.
© 2024 PatSnap. All rights reserved.Legal|Privacy policy|Modern Slavery Act Transparency Statement|Sitemap|About US| Contact US: help@patsnap.com