A control method for edge warping of hot-rolled steel plate
A hot-rolled steel plate and control method technology, applied in the direction of contour control, can solve the problems of increasing furnace time and energy consumption, affecting normal production output, slowing down production rhythm, etc., to improve product quality and yield, optimize two The effect of reducing the width distribution of vertical rollers and reducing the burning loss of slabs
- Summary
- Abstract
- Description
- Claims
- Application Information
AI Technical Summary
Problems solved by technology
Method used
Image
Examples
Embodiment 1
[0030] The method for controlling the edge warping of the hot-rolled steel plate comprises the following steps;
[0031] Step 1. Adjust and control the heating temperature of the hot-rolled steel plate slab to be 1190° C., and the heating time to be 200 minutes;
[0032] Step 2. Adjust the width reduction of the slab sizing machine to 30mm;
[0033] Step 3. Adjust the width reduction of the secondary vertical rollers as follows: the width reduction of the first pass of E1 is adjusted to 35.2mm, the width reduction of the second pass of E1 is adjusted to 32.7mm, and the width reduction of the first pass of E2 is adjusted to 28.3 mm, the width reduction in the second pass of E2 is adjusted to 6.6mm;
[0034] Step 4, adopting the adjusted temperature, time and width reduction amount to roll the hot-rolled steel plate slab.
Embodiment 2
[0036] The method for controlling the edge warping of the hot-rolled steel plate comprises the following steps;
[0037] Step 1. Adjust and control the heating temperature of the hot-rolled steel plate slab to be 1190° C., and the heating time to be 200 minutes;
[0038] Step 2. Adjust the width reduction of the slab sizing machine to 10mm;
[0039] Step 3. Adjust the width reduction of the secondary vertical rollers as follows: the width reduction of the first pass of E1 is adjusted to 35.2mm, the width reduction of the second pass of E1 is adjusted to 32.7mm, and the width reduction of the first pass of E2 is adjusted to 28.3 mm, the width reduction in the second pass of E2 is adjusted to 6.6mm;
[0040] Step 4, adopting the adjusted temperature, time and width reduction amount to roll the hot-rolled steel plate slab.
Embodiment 3
[0042] The method for controlling the edge warping of the hot-rolled steel plate comprises the following steps;
[0043] Step 1. Adjust and control the heating temperature of the hot-rolled steel plate slab to 1200° C., and the heating time to 200 minutes;
[0044] Step 2. Adjust the width reduction of the slab sizing machine to 100mm;
[0045] Step 3. Adjust the width reduction of the secondary vertical rollers as follows: the width reduction of the first pass of E1 is adjusted to 30mm, the width reduction of the second pass of E1 is adjusted to 30mm, the width reduction of the first pass of E2 is adjusted to 25mm, and the width reduction of the first pass of E2 is adjusted to 25mm. The width reduction of the second pass is adjusted to 1mm;
[0046] Step 4, adopting the adjusted temperature, time and width reduction amount to roll the hot-rolled steel plate slab.
PUM
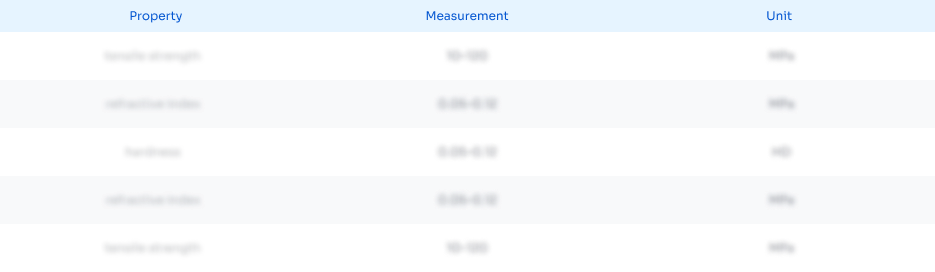
Abstract
Description
Claims
Application Information

- Generate Ideas
- Intellectual Property
- Life Sciences
- Materials
- Tech Scout
- Unparalleled Data Quality
- Higher Quality Content
- 60% Fewer Hallucinations
Browse by: Latest US Patents, China's latest patents, Technical Efficacy Thesaurus, Application Domain, Technology Topic, Popular Technical Reports.
© 2025 PatSnap. All rights reserved.Legal|Privacy policy|Modern Slavery Act Transparency Statement|Sitemap|About US| Contact US: help@patsnap.com