Fiber balance aerodynamic measuring system and method
A measurement system and measurement method technology, applied in the field of aerospace force measurement test, can solve the problems affecting the reliability of test data, temperature interference measurement error, output signal interference of resistance strain balance, etc., to meet the requirements of aerodynamic fine measurement Effect
- Summary
- Abstract
- Description
- Claims
- Application Information
AI Technical Summary
Problems solved by technology
Method used
Image
Examples
Embodiment 1
[0058] A kind of measurement method of above-mentioned fiber optic balance aerodynamic force measurement system, comprises the following steps:
[0059] Step 1. Combining the output signals of the fiber optic F-P strain gauges on each measuring beam of the fiber optic balance body to determine the output of each component of the fiber optic aerodynamic measurement balance;
[0060] In order to determine the output of each component of the fiber optic balance, it is necessary to combine the output signals of each fiber optic F-P strain gauge. Calculate the difference value of the output signal of the negative strain fiber optic strain gauge, and then sum each difference value as the output of this component,
[0061] Take the axial component of a three-component fiber optic balance as an example, see Figure 6-10 , which has two measuring beams n1, n2, four pairs of optical fiber strain gauges 11 and 12, 13 and 14, 15 and 16, 17 and 18 installed on the symmetrical positions of...
PUM
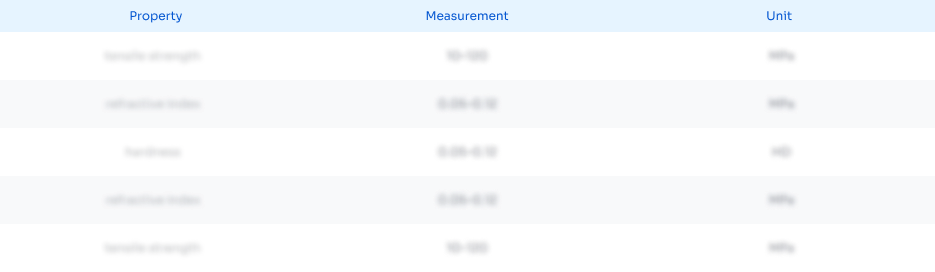
Abstract
Description
Claims
Application Information

- R&D Engineer
- R&D Manager
- IP Professional
- Industry Leading Data Capabilities
- Powerful AI technology
- Patent DNA Extraction
Browse by: Latest US Patents, China's latest patents, Technical Efficacy Thesaurus, Application Domain, Technology Topic, Popular Technical Reports.
© 2024 PatSnap. All rights reserved.Legal|Privacy policy|Modern Slavery Act Transparency Statement|Sitemap|About US| Contact US: help@patsnap.com