Bolt joint part looseness detecting method and system based on nonlinear shock excitation feature
A detection method and joint technology, applied in the direction of instruments, etc., can solve the problems of poor detection accuracy, nonlinear phenomenon, large measurement error, etc., and achieve the effects of flexible and convenient use, simple operation and wide applicability
- Summary
- Abstract
- Description
- Claims
- Application Information
AI Technical Summary
Problems solved by technology
Method used
Image
Examples
Embodiment Construction
[0025] Embodiments of the present invention are described in detail below, examples of which are shown in the drawings, wherein the same or similar reference numerals designate the same or similar elements or elements having the same or similar functions throughout. The embodiments described below by referring to the figures are exemplary and are intended to explain the present invention and should not be construed as limiting the present invention.
[0026] The realization principle of the present invention is that when the bolt joint is loose, the decrease of the pre-tightening force of the joint surface will cause the joint to present a strong nonlinear dynamic phenomenon, and as the loosening intensifies, the nonlinear characteristic is enhanced, and the energy is transferred from the fundamental frequency to Scatter toward higher harmonics, resulting in a proportional increase in the amplitude of higher harmonics. Therefore, the nonlinear excitation characteristic of the ...
PUM
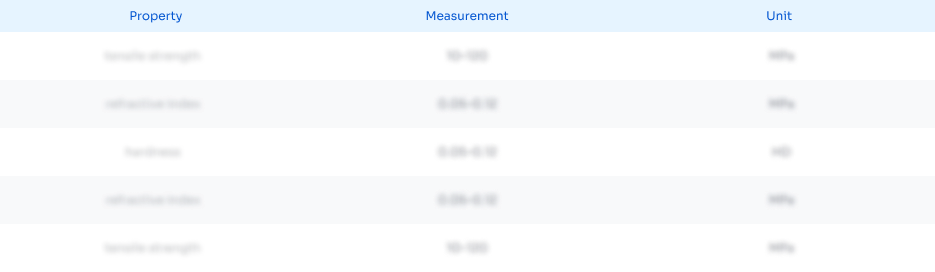
Abstract
Description
Claims
Application Information

- Generate Ideas
- Intellectual Property
- Life Sciences
- Materials
- Tech Scout
- Unparalleled Data Quality
- Higher Quality Content
- 60% Fewer Hallucinations
Browse by: Latest US Patents, China's latest patents, Technical Efficacy Thesaurus, Application Domain, Technology Topic, Popular Technical Reports.
© 2025 PatSnap. All rights reserved.Legal|Privacy policy|Modern Slavery Act Transparency Statement|Sitemap|About US| Contact US: help@patsnap.com