A Quasi-Zero Stiffness Vibration Isolator Using Multilayer Extruded Magnetic Springs and Swing Rods
A quasi-zero stiffness, vibration isolator technology, used in magnetic springs, springs/shock absorbers, springs, etc., can solve problems such as insufficient compact structure, small bearing capacity, and inability to meet a wide range of applications
- Summary
- Abstract
- Description
- Claims
- Application Information
AI Technical Summary
Problems solved by technology
Method used
Image
Examples
Embodiment Construction
[0025] The following will clearly and completely describe the technical solutions in the embodiments of the present invention with reference to the accompanying drawings in the embodiments of the present invention. Obviously, the described embodiments are only some, not all, embodiments of the present invention. Based on the embodiments of the present invention, all other embodiments obtained by persons of ordinary skill in the art without making creative efforts belong to the protection scope of the present invention.
[0026] The purpose of the present invention is to solve the problem that the existing quasi-zero stiffness vibration isolator is not compact enough, the bearing capacity is small, and cannot meet the wide range of application, and provides a multi-layer extruded magnetic spring and pendulum Quasi-zero stiffness vibration isolators for rods.
[0027] In order to make the above objects, features and advantages of the present invention more comprehensible, the pr...
PUM
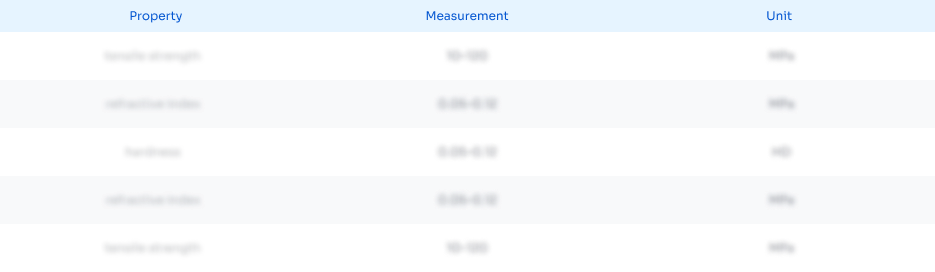
Abstract
Description
Claims
Application Information

- Generate Ideas
- Intellectual Property
- Life Sciences
- Materials
- Tech Scout
- Unparalleled Data Quality
- Higher Quality Content
- 60% Fewer Hallucinations
Browse by: Latest US Patents, China's latest patents, Technical Efficacy Thesaurus, Application Domain, Technology Topic, Popular Technical Reports.
© 2025 PatSnap. All rights reserved.Legal|Privacy policy|Modern Slavery Act Transparency Statement|Sitemap|About US| Contact US: help@patsnap.com