Hall signal sampling magnetoelectric encoder for suppressing interference and temperature drift
A magnetoelectric encoder and Hall signal technology, applied in the direction of transmitting sensing components, instruments, and converting sensor output using electric/magnetic devices, can solve problems such as low precision and angle delay of magnetoelectric encoders, and achieve improved The effect of measurement accuracy
- Summary
- Abstract
- Description
- Claims
- Application Information
AI Technical Summary
Problems solved by technology
Method used
Image
Examples
Embodiment 1
[0032] Embodiment 1, see attached figure 1 ,2.
[0033] A hall signal sampling magnetoelectric encoder for suppressing interference and temperature drift of the present invention includes an encoder support frame 3, one end 3-1 of the encoder support frame is fixedly connected to the motor flange 1-2, and the encoder supports The other end 3-2 of the frame is fixedly connected to the code disc 4 of the magnetoelectric encoder, and four Hall elements with a phase difference of 90° in turn are welded on the code disc 4 of the magnetoelectric encoder, respectively Hall sensor A1 and Hall sensor B1 , the Hall sensor A2, the Hall sensor B2 and the differential amplifier 9 are used for sampling, receiving and processing the magnetic field signal, and the motor shaft 1-1 is fixedly connected with the magnet 2 for generating the magnetic field signal. When the motor 1 rotates, it drives the magnet steel 2 to rotate, generating a changing magnetic field signal, which is fixed on the m...
Embodiment 2
[0034] Embodiment 2, see attached figure 1 ,2.
[0035] Others are the same as in Embodiment 1, the difference is that two differential signals will be obtained , It is directly reported to the processing unit of the servo control system. When the servo system needs the angle value, the arc tangent of the two signals is calculated in real time to obtain the angle value of the magnetoelectric encoder without delay.
PUM
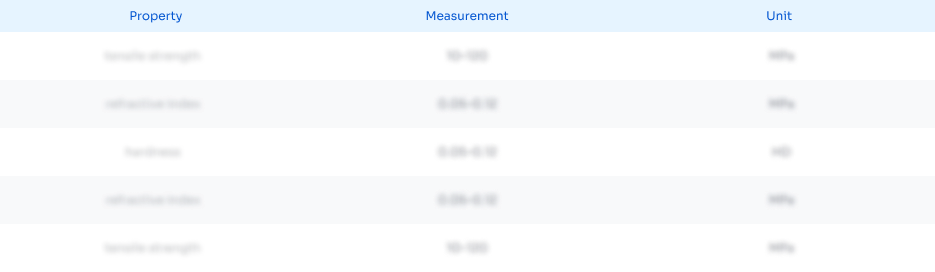
Abstract
Description
Claims
Application Information

- R&D
- Intellectual Property
- Life Sciences
- Materials
- Tech Scout
- Unparalleled Data Quality
- Higher Quality Content
- 60% Fewer Hallucinations
Browse by: Latest US Patents, China's latest patents, Technical Efficacy Thesaurus, Application Domain, Technology Topic, Popular Technical Reports.
© 2025 PatSnap. All rights reserved.Legal|Privacy policy|Modern Slavery Act Transparency Statement|Sitemap|About US| Contact US: help@patsnap.com