Gear teeth thickness measurement method based on line structured light
A technology of line structured light and gear teeth, which is applied in the direction of measuring devices, optical devices, instruments, etc., can solve the problems of slow measurement speed, probe wear radius compensation, difficult gear tooth thickness measurement, etc., to improve measurement efficiency, The effect of reducing random errors and fast measurement speed
- Summary
- Abstract
- Description
- Claims
- Application Information
AI Technical Summary
Problems solved by technology
Method used
Image
Examples
Embodiment Construction
[0061] A gear tooth thickness measurement method based on line structured light will be further described below with reference to the accompanying drawings. like Figure 6 , this method can be applied to both the vertical measuring machine and the horizontal measuring machine, and the vertical measuring machine is taken as an example for illustration.
[0062] The vertical measuring machine includes a spindle unit, a measuring unit and a machine bed, and the spindle unit and the measuring unit are installed on the bed. The spindle unit includes the spindle and fixed chuck, θ 1 The axial circular grating is connected to the main shaft; the surveying unit includes a Z-direction moving rod, an X-direction moving rod, an angle adjustment arm and a structured light probe. The Z-axis grating is installed on the measuring X-direction moving rod to measure the movement of the Z-axis. Measure the movement of the surveying unit along the X direction on the Z axis, the angle adjustment...
PUM
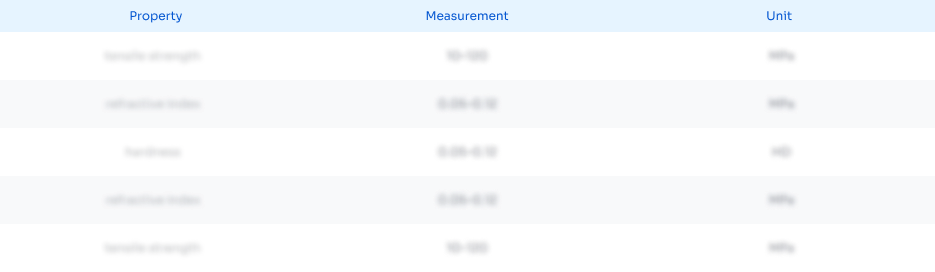
Abstract
Description
Claims
Application Information

- R&D
- Intellectual Property
- Life Sciences
- Materials
- Tech Scout
- Unparalleled Data Quality
- Higher Quality Content
- 60% Fewer Hallucinations
Browse by: Latest US Patents, China's latest patents, Technical Efficacy Thesaurus, Application Domain, Technology Topic, Popular Technical Reports.
© 2025 PatSnap. All rights reserved.Legal|Privacy policy|Modern Slavery Act Transparency Statement|Sitemap|About US| Contact US: help@patsnap.com