Impulse type secondary jet flow thrust vector control system
A technology of thrust vector control and secondary jet, applied in jet propulsion devices, rocket engine devices, machines/engines, etc., can solve the problem of increasing secondary flow channels and Coanda effect surfaces, increasing system complexity, structural quality and size and other problems, to achieve the effects of enhanced deflection ability, reduced secondary flow, and low energy consumption
- Summary
- Abstract
- Description
- Claims
- Application Information
AI Technical Summary
Problems solved by technology
Method used
Image
Examples
Embodiment Construction
[0023] The present invention will be further described in detail below in conjunction with examples, but the embodiments of the present invention are not limited thereto.
[0024] Such as figure 1 As shown, a pulse type secondary jet thrust vector control system of the present invention includes a rocket engine 1, an annular high-pressure gas storage tank 2, a gas pipeline 3, a pressure stabilizing valve 4, a gas collection chamber 5, a pulse jet control valve 6, Jet nozzle 7 and engine nozzle 8.
[0025] For the rocket engine using the Laval nozzle, the annular high-pressure gas storage tank 2 is set in the peripheral space corresponding to the throat of the engine nozzle 8, and is used as the working medium source of the secondary jet. Transport the secondary jet working medium; filter and adjust the pressure of the secondary jet working medium through the pressure stabilizing valve 4 equipped on the gas pipeline 3; the gas collection chamber 5 is welded on the diffusion se...
PUM
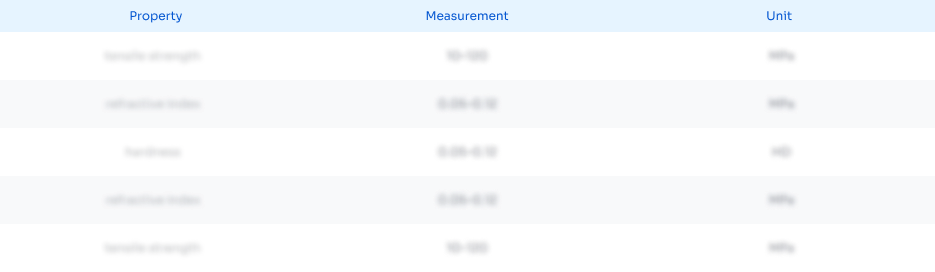
Abstract
Description
Claims
Application Information

- R&D Engineer
- R&D Manager
- IP Professional
- Industry Leading Data Capabilities
- Powerful AI technology
- Patent DNA Extraction
Browse by: Latest US Patents, China's latest patents, Technical Efficacy Thesaurus, Application Domain, Technology Topic, Popular Technical Reports.
© 2024 PatSnap. All rights reserved.Legal|Privacy policy|Modern Slavery Act Transparency Statement|Sitemap|About US| Contact US: help@patsnap.com