Pressure tracking valve controlled shield pushing hydraulic system
A technology of hydraulic system and tracking valve, which is used in fluid pressure actuating devices, mining equipment, earth-moving drilling, etc., can solve the problems of long adjustment time, complex system, and inability to realize coordinated control of the pressure of the propulsion cylinder, and improve reliability. performance, reducing control elements, improving responsiveness and efficiency
- Summary
- Abstract
- Description
- Claims
- Application Information
AI Technical Summary
Problems solved by technology
Method used
Image
Examples
Embodiment Construction
[0013] The present invention will be further described below in conjunction with drawings and embodiments.
[0014] As shown in the drawings, the present invention includes: any number of propulsion partitions and fuel tanks 27 with the same structure; each propulsion partition includes a main control oil cylinder hydraulic branch system and any number of pressure tracking valve control oil cylinder hydraulic branch systems; the main control The cylinder hydraulic branch system includes: proportional speed regulating valve 1, proportional pressure reducing valve 2, first one-way valve 3, first overflow valve 4, first two-way cartridge valve 5, first two-way three-way reversing valve Valve 6, the second two-way cartridge valve 7, the second two-position three-way reversing valve 8, the second one-way valve 9, the third one-way valve 10, the third two-way cartridge valve 11, the third two-position Three-way reversing valve 12, propulsion cylinder 13 with built-in displacement se...
PUM
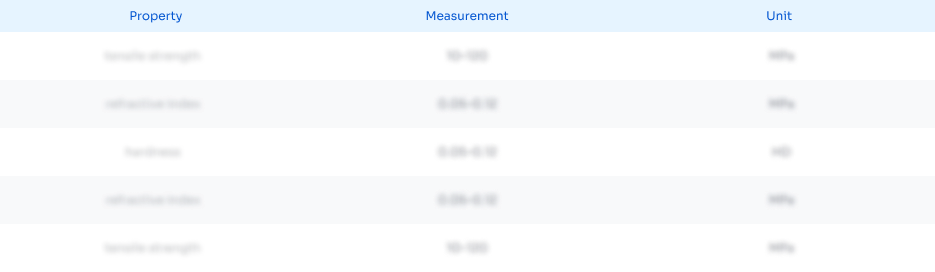
Abstract
Description
Claims
Application Information

- R&D
- Intellectual Property
- Life Sciences
- Materials
- Tech Scout
- Unparalleled Data Quality
- Higher Quality Content
- 60% Fewer Hallucinations
Browse by: Latest US Patents, China's latest patents, Technical Efficacy Thesaurus, Application Domain, Technology Topic, Popular Technical Reports.
© 2025 PatSnap. All rights reserved.Legal|Privacy policy|Modern Slavery Act Transparency Statement|Sitemap|About US| Contact US: help@patsnap.com