Axisymmetric silicon micromechanical gyroscope sensitive structure and manufacturing method thereof
A silicon micromechanical and sensitive structure technology, applied in gyroscope/steering sensing equipment, gyro effect for speed measurement, measuring device, etc., can solve the problems of severe structural coupling, asymmetric motion of the mass block support beam, etc., and achieve reduction Effects of stress concentration, improvement of mechanical sensitivity, and high sensitivity
- Summary
- Abstract
- Description
- Claims
- Application Information
AI Technical Summary
Problems solved by technology
Method used
Image
Examples
Embodiment Construction
[0034] Such as figure 1 As shown, the sensitive structure of the axisymmetric silicon micromachined gyroscope in this embodiment includes an elastic frame 1 made of silicon wafers. The two sides of the elastic frame 1 are provided with bonded anchor points 2 arranged symmetrically, and the elastic frame 1 is provided with axisymmetric The through-hole area, and the symmetry axis of the through-hole area is provided with an "H"-shaped support beam 3, and two sides of the "H"-shaped support beam 3 are respectively provided with two axisymmetric shafts relative to the "H"-shaped support beam 3. Two sensitive mass blocks 4 (as movable capacitor plates), and the sensitive mass blocks 4 are arranged in the through-hole area and one side is connected to the "H"-shaped support beam 3 through the connecting beam 5 . In this embodiment, the elastic frame 1 is used as the stress release structure in the structural design of the micro-gyroscope. The elastic frame 1 is cleverly designed an...
PUM
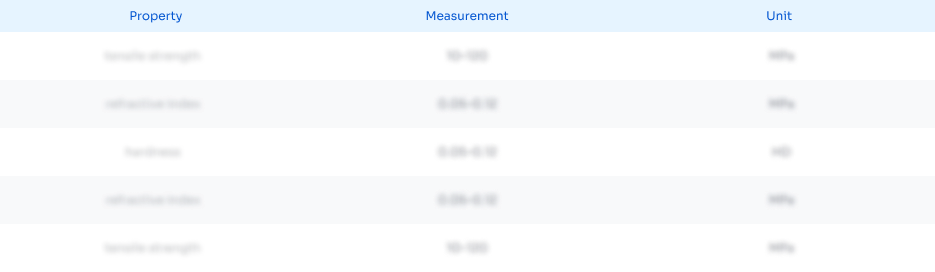
Abstract
Description
Claims
Application Information

- R&D
- Intellectual Property
- Life Sciences
- Materials
- Tech Scout
- Unparalleled Data Quality
- Higher Quality Content
- 60% Fewer Hallucinations
Browse by: Latest US Patents, China's latest patents, Technical Efficacy Thesaurus, Application Domain, Technology Topic, Popular Technical Reports.
© 2025 PatSnap. All rights reserved.Legal|Privacy policy|Modern Slavery Act Transparency Statement|Sitemap|About US| Contact US: help@patsnap.com