An energy-saving and efficient printing and dyeing process
A printing and dyeing process and high-efficiency technology, applied in the direction of dyeing, textile material processing, liquid/gas/vapor removal, etc., can solve the problems of large impurities or acidic substances, low work efficiency, high moisture content in fabrics, etc. Water squeezing effect, energy saving, high coloring effect
- Summary
- Abstract
- Description
- Claims
- Application Information
AI Technical Summary
Problems solved by technology
Method used
Image
Examples
Embodiment 1
[0037] An energy-saving and high-efficiency printing and dyeing process, including the following steps: (1) Singeing: lay out the gray cloth to be dyed and sew the outer edges together manually, and then send the sewn gray cloth to the burner. The singeing treatment is carried out in the wool machine to remove the burrs and hair balls of the gray cloth. The singeing machine is an existing technology and will not be described again; (2) Soaking and cleaning: put the singeed gray cloth into the Nacl solution for cleaning. soaking, wherein the concentration of the Nacl solution is 2mol / L, and then the cloth is cleaned with deionized water; (3) Dyeing: the cloth is bleached first, and the washed gray cloth is first sent to the bleaching tank, Soaking in bleaching solution, wherein the bleaching solution includes the following components in parts by weight: 10 parts of hydrogen peroxide, 5 parts of hydroxyethylidene diphosphonic acid, 6 parts of ammonium borate, and 3 parts of sodiu...
Embodiment 2
[0047] An energy-saving and high-efficiency printing and dyeing process, including the following steps: (1) Singeing: lay out the gray cloth to be dyed and sew the outer edges together manually, and then send the sewn gray cloth to the burner. The singeing treatment is carried out in the wool machine to remove the burrs and hair balls of the gray cloth. The singeing machine is an existing technology and will not be described again; (2) Soaking and cleaning: put the singeed gray cloth into the Nacl solution for cleaning. soaking, wherein the concentration of the Nacl solution is 4mol / L, and then the cloth is cleaned with deionized water; (3) Dyeing: the cloth is bleached first, and the washed gray cloth is first sent to the bleaching tank, Soaking treatment is carried out in the bleaching solution, wherein the bleaching solution includes the following components in parts by weight: 20 parts of hydrogen peroxide, 12 parts of hydroxyethylidene diphosphonic acid, 8 parts of ammoniu...
Embodiment 3
[0050] An energy-saving and high-efficiency printing and dyeing process, including the following steps: (1) Singeing: lay out the gray cloth to be dyed and sew the outer edges together manually, and then send the sewn gray cloth to the burner. The singeing treatment is carried out in the wool machine to remove the burrs and hair balls of the gray cloth. The singeing machine is an existing technology and will not be described again; (2) Soaking and cleaning: put the singeed gray cloth into the Nacl solution for cleaning. soaking, wherein the concentration of the Nacl solution is 2mol / L, and then the cloth is cleaned with deionized water; (3) Dyeing: the cloth is bleached first, and the washed gray cloth is first sent to the bleaching tank, Soaking treatment is carried out in the bleaching solution, wherein the bleaching solution includes the following components in parts by weight: 15 parts of hydrogen peroxide, 8 parts of hydroxyethylidene diphosphonic acid, 6 parts of ammonium...
PUM
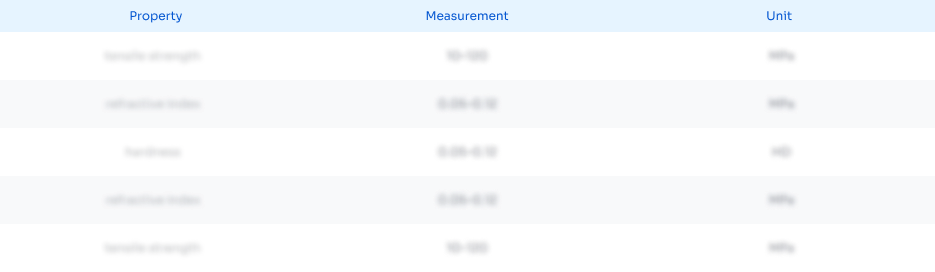
Abstract
Description
Claims
Application Information

- R&D
- Intellectual Property
- Life Sciences
- Materials
- Tech Scout
- Unparalleled Data Quality
- Higher Quality Content
- 60% Fewer Hallucinations
Browse by: Latest US Patents, China's latest patents, Technical Efficacy Thesaurus, Application Domain, Technology Topic, Popular Technical Reports.
© 2025 PatSnap. All rights reserved.Legal|Privacy policy|Modern Slavery Act Transparency Statement|Sitemap|About US| Contact US: help@patsnap.com