Combustion system with dry mud directly input into boiler
A dry mud and direct technology, applied in the direction of incinerators, combustion methods, combustion types, etc., can solve problems such as coal breaking, blockage, and difficulty in boiler slag discharge, and achieve the effect of reducing disturbance and improving incineration efficiency
- Summary
- Abstract
- Description
- Claims
- Application Information
AI Technical Summary
Problems solved by technology
Method used
Image
Examples
Embodiment Construction
[0014] In order to make the object, technical solution and advantages of the present invention clearer, the present invention will be further described in detail below in conjunction with specific embodiments. It should be understood that the specific embodiments described here are only used to explain the present invention, and are not intended to limit the present invention.
[0015] see figure 1 and figure 2 , this specific embodiment discloses a dry slime incineration system directly into the furnace, including a hopper 1, a conveyor belt 2, a coal conveying system 3, a mud conveying system 4, a coal slime conversion platform 5 and a boiler 6, the coal conveying system 3 and the coal conveying system The mud system 4 is respectively connected to the coal slime conversion platform 5 through a three-way connection. During use, the coal conveying system 3 and the mud conveying system 4 are respectively connected by rotating the three-way to convey the mud cake or coal cake....
PUM
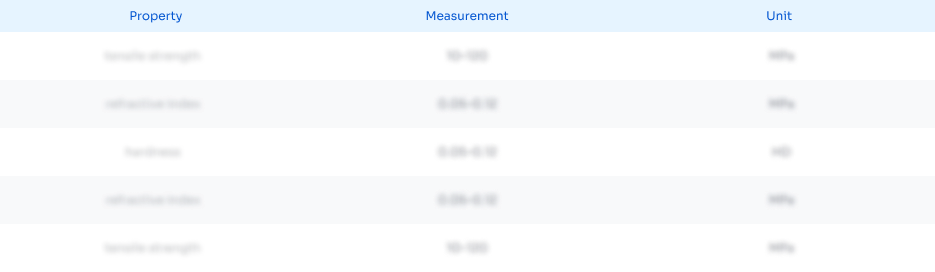
Abstract
Description
Claims
Application Information

- R&D Engineer
- R&D Manager
- IP Professional
- Industry Leading Data Capabilities
- Powerful AI technology
- Patent DNA Extraction
Browse by: Latest US Patents, China's latest patents, Technical Efficacy Thesaurus, Application Domain, Technology Topic, Popular Technical Reports.
© 2024 PatSnap. All rights reserved.Legal|Privacy policy|Modern Slavery Act Transparency Statement|Sitemap|About US| Contact US: help@patsnap.com