Method for thermal control multilayer coating of induction type magnetometer
A multi-layer coating and magnetometer technology, which is applied in the direction of the size/direction of the magnetic field, can solve problems such as the inability to fix multi-layer coatings, the inability to overlap adjacent multi-layers, and the impact on the performance of the induction magnetometer.
- Summary
- Abstract
- Description
- Claims
- Application Information
AI Technical Summary
Problems solved by technology
Method used
Image
Examples
Embodiment
[0045] The implementation steps of this embodiment are specifically as follows:
[0046] 1. First, make the polyimide bottom film
[0047] (1) Place the inductive magnetometer on a piece of white paper with the end of the dendritic sensor as the contact point;
[0048] (2) Draw a triangle with three contact points as vertices on the white paper;
[0049] (3) change the contact point of dendritic sensor end and blank paper, draw all three contact points as the triangle that apex forms successively according to step (2), thus draw the outer contour dimension figure of whole dendritic structure sensor;
[0050] (4) two layers of 100 micron polyimide film materials are pasted together to form a polyimide base film with a thickness of 200 microns;
[0051] (5) Cut the polyimide base film according to the triangle size formed in step (3), and each triangle surface corresponds to a separate polyimide base film.
[0052] 2. Multi-layer production
[0053](1) 20 units of multi-laye...
PUM
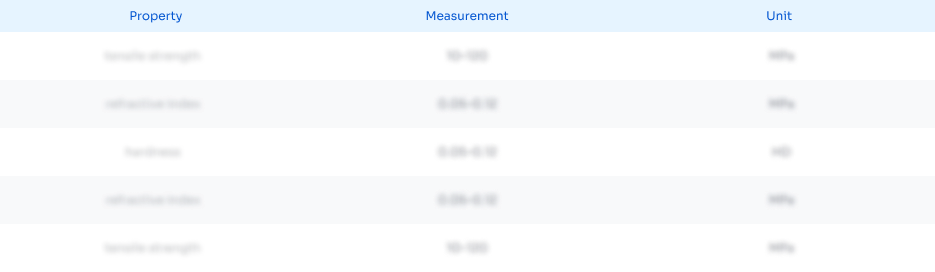
Abstract
Description
Claims
Application Information

- Generate Ideas
- Intellectual Property
- Life Sciences
- Materials
- Tech Scout
- Unparalleled Data Quality
- Higher Quality Content
- 60% Fewer Hallucinations
Browse by: Latest US Patents, China's latest patents, Technical Efficacy Thesaurus, Application Domain, Technology Topic, Popular Technical Reports.
© 2025 PatSnap. All rights reserved.Legal|Privacy policy|Modern Slavery Act Transparency Statement|Sitemap|About US| Contact US: help@patsnap.com