Integrated type magneto-rheological damper with built-in distance sensors for displacement detection
A distance sensor, displacement detection technology, applied in shock absorbers, shock absorbers, springs/shock absorbers, etc., can solve the problem of affecting the overall reliability and stability of the vibration control system, increase the volume of the control system, and shorten the service life of the system and other problems, to achieve the effect of improving reliability and stability, reducing system volume, and optimizing vibration reduction effect.
- Summary
- Abstract
- Description
- Claims
- Application Information
AI Technical Summary
Problems solved by technology
Method used
Image
Examples
Embodiment Construction
[0014] Below in conjunction with accompanying drawing and embodiment the present invention will be further described:
[0015] figure 1 It is a structural schematic diagram of the present invention, mainly including left lug 1, piston rod 2, dust cover 3, capacitive distance sensor I4, capacitive distance sensor II5, damper left end cover 6, damper cylinder 7, piston head 8 , Excitation coil 9, nut 10, floating piston 11, damper right end cover 12 and right lifting lug 13.
[0016] figure 2 It is a partial schematic diagram when the piston head of the present invention moves to the rightmost end of the stroke. At this time, the radial radial gap between the capacitive distance sensor and the dust cover is the smallest, that is, the attached figure 2 shown h min .
[0017] image 3 It is a partial schematic diagram when the piston head of the present invention moves to the leftmost end of the stroke. At this time, the radial gap between the capacitive distance sensor an...
PUM
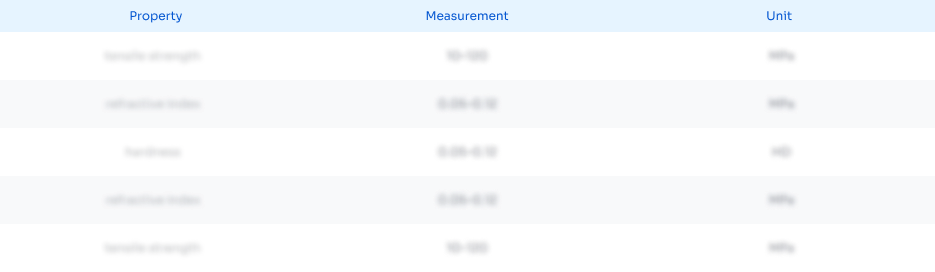
Abstract
Description
Claims
Application Information

- Generate Ideas
- Intellectual Property
- Life Sciences
- Materials
- Tech Scout
- Unparalleled Data Quality
- Higher Quality Content
- 60% Fewer Hallucinations
Browse by: Latest US Patents, China's latest patents, Technical Efficacy Thesaurus, Application Domain, Technology Topic, Popular Technical Reports.
© 2025 PatSnap. All rights reserved.Legal|Privacy policy|Modern Slavery Act Transparency Statement|Sitemap|About US| Contact US: help@patsnap.com