Duplex Cold Rolling Line
A composite cold rolling line technology, applied in metal rolling, metal rolling, workpiece surface treatment equipment, etc., can solve the problem of long rolling time, reduction of subsequent cold rolling mill rolling cuts, high rolling reduction rate, etc. question
- Summary
- Abstract
- Description
- Claims
- Application Information
AI Technical Summary
Problems solved by technology
Method used
Image
Examples
Embodiment Construction
[0020] The present invention will be described in detail below in conjunction with the accompanying drawings and embodiments.
[0021] refer to figure 2 , an embodiment of the composite cold-rolling line 1 of the present invention, is used for making the input black skin coil (Blackcoil) into a large number of cold-rolled thin-hard plate coils (Cold Rolled coil) continuously, and the composite cold-rolling Line 1 includes a feeding unit 2, a first rolling unit 3, an annealing and rust removal unit 4, a pickling unit 5, a stripping unit 6, and a second rolling unit in sequence from upstream to downstream of the production line 7. A material returning unit 8, and a material accumulating unit 9 arranged between the aforementioned units and used for connection according to the matching of production speed. The feeding unit 2 includes a feeding area 21 , and a first welding machine 22 downstream of the feeding area 21 . In this embodiment, the feeding area 21 has two uncoiling s...
PUM
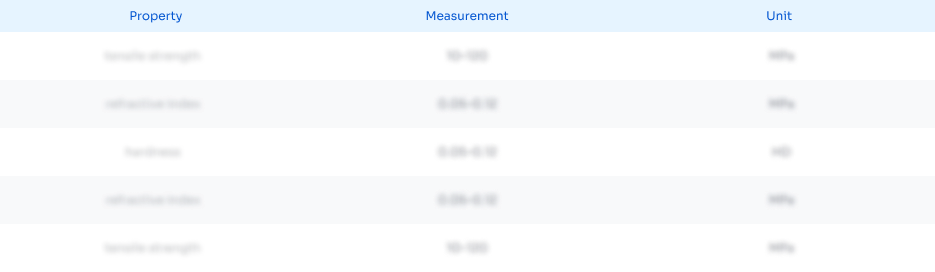
Abstract
Description
Claims
Application Information

- R&D
- Intellectual Property
- Life Sciences
- Materials
- Tech Scout
- Unparalleled Data Quality
- Higher Quality Content
- 60% Fewer Hallucinations
Browse by: Latest US Patents, China's latest patents, Technical Efficacy Thesaurus, Application Domain, Technology Topic, Popular Technical Reports.
© 2025 PatSnap. All rights reserved.Legal|Privacy policy|Modern Slavery Act Transparency Statement|Sitemap|About US| Contact US: help@patsnap.com