Method considering axial deformation for calculating time-varying meshing stiffness of helical gear
A technology of helical cylindrical gears and time-varying meshing stiffness, which is applied in calculation, design optimization/simulation, special data processing applications, etc., can solve problems such as low calculation accuracy and does not consider the influence of time-varying meshing stiffness, and achieve accuracy improvement Effect
- Summary
- Abstract
- Description
- Claims
- Application Information
AI Technical Summary
Problems solved by technology
Method used
Image
Examples
Embodiment Construction
[0026] The present invention will be further described in detail below in conjunction with the accompanying drawings and taking the structural parameters of the helical spur gear shown in Table 1 as an example.
[0027] Table 1
[0028]
[0029]
[0030] refer to figure 1 , a calculation method for time-varying mesh stiffness of helical cylindrical gears considering axial deformation, including the following steps:
[0031] Step 1) Calculate the end face bending stiffness dk of the helical cylindrical gear tooth slice tb , end face shear stiffness value dk ts , radial compression stiffness value dk ta and face tooth base stiffness value dk tf ;
[0032] Step 1.1) Based on the slice theory, the teeth of the helical cylindrical gear are divided into multiple slices of width dl along the tooth width direction, and the meshing force F perpendicular to any slice is decomposed to obtain the end face meshing force F of the slice t and axial meshing force F a , and then t...
PUM
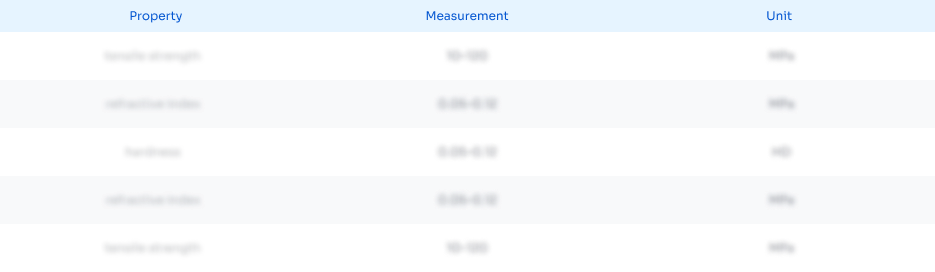
Abstract
Description
Claims
Application Information

- Generate Ideas
- Intellectual Property
- Life Sciences
- Materials
- Tech Scout
- Unparalleled Data Quality
- Higher Quality Content
- 60% Fewer Hallucinations
Browse by: Latest US Patents, China's latest patents, Technical Efficacy Thesaurus, Application Domain, Technology Topic, Popular Technical Reports.
© 2025 PatSnap. All rights reserved.Legal|Privacy policy|Modern Slavery Act Transparency Statement|Sitemap|About US| Contact US: help@patsnap.com