Robot system for rapidly harvesting bunch of grapes without falling and realization method thereof
A robotic system, non-shedding technology, applied in the direction of picking machines, harvesters, agricultural machinery and implements, etc., can solve the problem of rapid and non-shedding picking of grape bunches, adverse effects on the quality of the bunches on the market and storage period, and vibration reduction. The results are limited and other problems, to achieve the effect of realizing fast and non-dropping robot harvesting operation, shortening the path and time of fruit transfer and release, and reducing the risk of fruit drop off
- Summary
- Abstract
- Description
- Claims
- Application Information
AI Technical Summary
Problems solved by technology
Method used
Image
Examples
Embodiment Construction
[0024] The technical solutions of the present invention will be described in further detail below in conjunction with the accompanying drawings and specific embodiments.
[0025] like figure 1 As shown, the robot system for quickly and non-shedding grape harvesting consists of a mobile chassis 1, a lifting mechanism 2, an aerial fruit box device and a light and small harvesting manipulator. The bottom of the lifting mechanism 2 is installed on the mobile chassis 1, and the fruit box device in the air and the harvesting manipulator are installed on the top of the lifting mechanism 2.
[0026] The lifting mechanism 2 sends the aerial fruit box device and the light and small harvesting manipulator to the corresponding height zone where the grape bunches 16 grow, and the light and small harvesting manipulator completes the picking, transferring and putting into the grape bunches 16 into the fruit box. Action, the light and small harvesting manipulator puts the picked grape bunche...
PUM
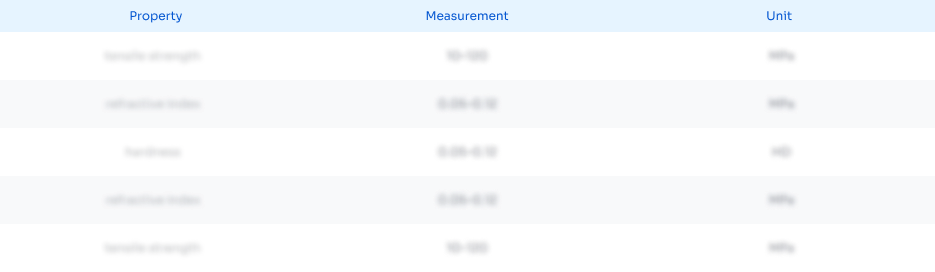
Abstract
Description
Claims
Application Information

- Generate Ideas
- Intellectual Property
- Life Sciences
- Materials
- Tech Scout
- Unparalleled Data Quality
- Higher Quality Content
- 60% Fewer Hallucinations
Browse by: Latest US Patents, China's latest patents, Technical Efficacy Thesaurus, Application Domain, Technology Topic, Popular Technical Reports.
© 2025 PatSnap. All rights reserved.Legal|Privacy policy|Modern Slavery Act Transparency Statement|Sitemap|About US| Contact US: help@patsnap.com