A sensorless permanent magnet synchronous motor rotor position detection method
- Summary
- Abstract
- Description
- Claims
- Application Information
AI Technical Summary
Problems solved by technology
Method used
Image
Examples
Embodiment Construction
[0033] During the rotation of the permanent magnet synchronous motor rotor, the winding will generate a back electromotive force due to cutting the magnetic force line, and the back electromotive force has a direct correspondence with the rotor phase, so the back electromotive force information can be used to monitor the phase of the rotor. During the operation of the motor, the amplitude of the reverse electromotive force is used to determine the phases of the rotor. The implementation method is complicated. On the one hand, there are high-frequency components in the currents of each phase. On the other hand, when the speed is unstable, the back electromotive force itself is also unstable. Therefore, it is not suitable to convert the rotor phase directly from the magnitude of the back electromotive force. The method of signal processing can be used to digitally process the change process of the back electromotive force of the three-phase winding, and extract some relatively sta...
PUM
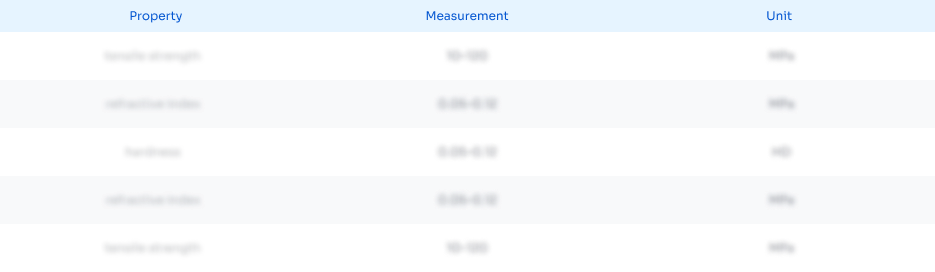
Abstract
Description
Claims
Application Information

- R&D
- Intellectual Property
- Life Sciences
- Materials
- Tech Scout
- Unparalleled Data Quality
- Higher Quality Content
- 60% Fewer Hallucinations
Browse by: Latest US Patents, China's latest patents, Technical Efficacy Thesaurus, Application Domain, Technology Topic, Popular Technical Reports.
© 2025 PatSnap. All rights reserved.Legal|Privacy policy|Modern Slavery Act Transparency Statement|Sitemap|About US| Contact US: help@patsnap.com