Light projection measurement device and method for axial clearance of movable and stationary blades of engine
A technology of axial clearance and measurement method, applied in mechanical measurement devices, measurement devices, optical devices, etc., to achieve the effect of low intervention and high measurement accuracy
- Summary
- Abstract
- Description
- Claims
- Application Information
AI Technical Summary
Problems solved by technology
Method used
Image
Examples
Embodiment Construction
[0021] The technical scheme adopted by the present invention is an axial measurement system for moving and stationary blades of an engine based on the light projection method, the schematic diagram of the system is shown in figure 1 . The system includes the following modules:
[0022] Optical path system module: This module requires a strong parallel white light source with a divergence angle of less than 1° and uniform distribution of light intensity. The size of the light spot is larger than the size of the casing opening, and the diameter of the casing opening is also larger than the gap between the moving blade and the stationary blade. As well as the range of variation, a suitable lens group or lens makes the light spot image on the line array / area array CCD surface of the photoelectric sensor device.
[0023] Area array / linear array CCD signal acquisition module: This module includes area array or linear array CCD sensor, CCD signal drive module (can be driven by CPLD,...
PUM
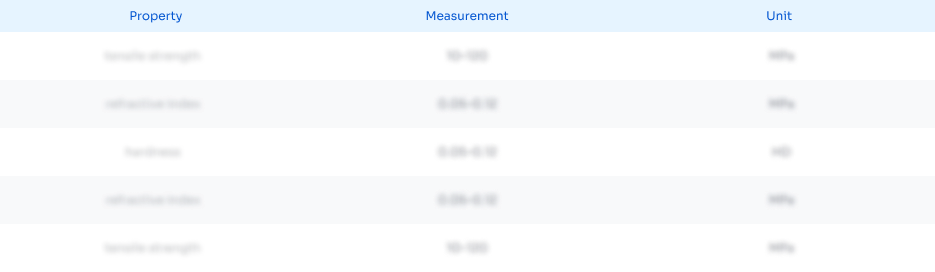
Abstract
Description
Claims
Application Information

- Generate Ideas
- Intellectual Property
- Life Sciences
- Materials
- Tech Scout
- Unparalleled Data Quality
- Higher Quality Content
- 60% Fewer Hallucinations
Browse by: Latest US Patents, China's latest patents, Technical Efficacy Thesaurus, Application Domain, Technology Topic, Popular Technical Reports.
© 2025 PatSnap. All rights reserved.Legal|Privacy policy|Modern Slavery Act Transparency Statement|Sitemap|About US| Contact US: help@patsnap.com