Flexible constraint layer for laser shock reinforcement online repair and manufacturing method of flexible constraint layer
A technology of laser shock strengthening and manufacturing method, which is applied in the field of flexible constrained layers, can solve the problems that the surface shape of metal components is limited to a plane, cannot adapt to various complex surface shapes, and increases costs, so as to improve the effect of laser shock and the scope of engineering applications Wide, the effect of engineering application cost reduction
- Summary
- Abstract
- Description
- Claims
- Application Information
AI Technical Summary
Problems solved by technology
Method used
Image
Examples
Embodiment
[0060] attached figure 1 It is a schematic diagram of laminating the flexible constrained layer and the absorbing layer, figure 1 Among them, 1-flexible constrained layer, 2-energy absorbing layer. In this embodiment, the flexible constrained layer is made of bisphenol A epoxy resin and cycloaliphatic amine curing agent according to the formula of 1.5:1 and cured.
[0061] attached figure 2 Flowchart for the fabrication of flexible constrained layer materials. attached image 3 Schematic diagram of the three-layer board mold explosion for making the flexible constrained layer, image 3 Middle, 3-backing plate, 4-setting template. attached Figure 4 Colloid diagram for the semi-cured flexible constrained layer. attached Figure 5 The rendering of the flexible constrained layer applied to the damaged area of the complex surface, Figure 5 Among them, 1-flexible constrained layer, 2-energy absorbing layer, 5-damage component.
[0062] Attached below Figure 2-5 Desc...
PUM
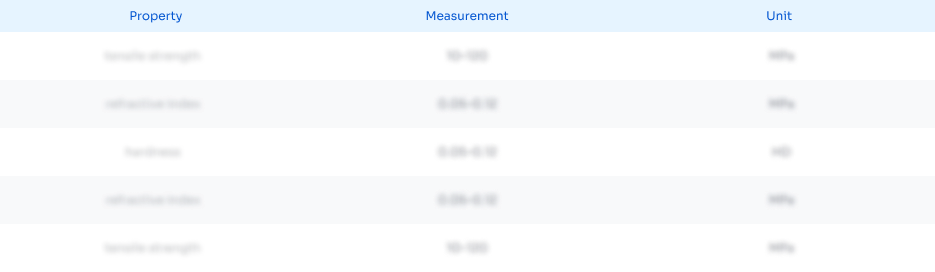
Abstract
Description
Claims
Application Information

- R&D
- Intellectual Property
- Life Sciences
- Materials
- Tech Scout
- Unparalleled Data Quality
- Higher Quality Content
- 60% Fewer Hallucinations
Browse by: Latest US Patents, China's latest patents, Technical Efficacy Thesaurus, Application Domain, Technology Topic, Popular Technical Reports.
© 2025 PatSnap. All rights reserved.Legal|Privacy policy|Modern Slavery Act Transparency Statement|Sitemap|About US| Contact US: help@patsnap.com