Intelligent injection molding forming equipment
An injection molding and intelligent technology, applied in the field of intelligent injection molding equipment, can solve problems such as waste and energy loss, and achieve the effects of reducing energy consumption, reducing energy loss, and reducing production costs
- Summary
- Abstract
- Description
- Claims
- Application Information
AI Technical Summary
Problems solved by technology
Method used
Image
Examples
Embodiment 1
[0031] Such as figure 1 As shown, the present invention provides an intelligent injection molding equipment. The injection molding system includes several mold components 1, several high-pressure mold clamping units 2, several mobile injection molding units 3, several retrieving units 4, intelligent conveying And positioning unit 5 and control unit;
[0032] The mold assembly 1 includes a mold and a low-pressure mold clamping mechanism, and the low-pressure mold clamping mechanism can lock the mold when transporting the mold; the control unit can call the corresponding process of the mold for injection molding; the high-pressure clamping mechanism can The mold unit 2 can lock the mold assembly 1 according to the corresponding mold clamping process requirements; the mobile injection unit 3 can inject glue into the mold assembly 1 according to the corresponding injection molding process requirements; the material taking unit 4 can open the mold and take out the molded plastic p...
Embodiment 2
[0052] combine figure 1 , the present invention provides an intelligent injection molding equipment, the injection molding system includes a number of mold components 1, a number of high-pressure mold clamping units 2, a number of mobile injection molding units 3, a number of retrieving units 4, intelligent conveying and positioning unit 5 and control unit;
[0053] The mold assembly 1 includes a mold and a low-pressure mold clamping mechanism, and the low-pressure mold clamping mechanism can lock the mold when transporting the mold; the control unit can call the corresponding process of the mold for injection molding; the high-pressure clamping mechanism can The mold unit 2 can lock the mold assembly 1 according to the corresponding mold clamping process requirements; the mobile injection unit 3 can inject glue into the mold assembly 1 according to the corresponding injection molding process requirements; the material taking unit 4 can open the mold and take out the molded p...
PUM
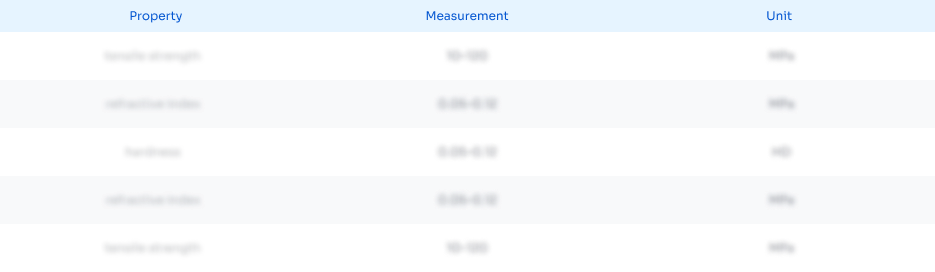
Abstract
Description
Claims
Application Information

- R&D
- Intellectual Property
- Life Sciences
- Materials
- Tech Scout
- Unparalleled Data Quality
- Higher Quality Content
- 60% Fewer Hallucinations
Browse by: Latest US Patents, China's latest patents, Technical Efficacy Thesaurus, Application Domain, Technology Topic, Popular Technical Reports.
© 2025 PatSnap. All rights reserved.Legal|Privacy policy|Modern Slavery Act Transparency Statement|Sitemap|About US| Contact US: help@patsnap.com