UV (ultraviolet) fire retardant coating and preparation method thereof
A technology of fire-resistant coatings and raw materials, applied in fire-resistant coatings, anti-fouling/underwater coatings, polyester coatings, etc., can solve the problem of poor flame-retardant performance, poor water resistance, poor oil resistance and weather resistance of UV fire-resistant coatings, and decline in mechanical properties of coatings, etc. problems, achieve excellent antibacterial and self-cleaning properties, fast curing speed, and convenient construction
- Summary
- Abstract
- Description
- Claims
- Application Information
AI Technical Summary
Problems solved by technology
Method used
Image
Examples
Embodiment 1
[0023] 1. Preparation of flame-retardant modified fluorine-containing hyperbranched polyurethane-epoxy acrylic resin copolymer.
[0024] Step 1. Add 30g of 9,10-dihydro-9-oxa-10-phosphaphenanthrene-10-oxide (DOPO) and 150mL of dioxane (AR) into a 250mL four-necked flask, blow nitrogen gas and Stir and heat up to 90°C, after DOPO is completely dissolved, start to drop 15g of HOCH 2 CF 2 O(CF 2 CF 2 O) 15 (CF 2 O) 15 CF 2 CH 2 OH perfluoropolyether diol (ZDOL) with stirring, the ZDOL dropping speed is 0.8mL / min, and the stirring speed is 300r / min. After the dropping is completed, the temperature is raised to 80°C, and the reactant is rotated for 1 hour to recover the dioxygen. Hexacyclic, the viscous product was obtained after the reaction, and then washed 5 times with absolute ethanol, and vacuum-dried at 70°C for 7 hours to obtain the modified flame retardant DOPO-ZDOL; for the synthesis mechanism diagram of DOPO-ZDOL, see figure 1 .
[0025] Step 2. In a 500mL thre...
Embodiment 2
[0030] 1. Preparation of flame-retardant modified fluorine-containing hyperbranched polyurethane-epoxy acrylic resin copolymer:
[0031] Step 1. Add 20g of 9,10-dihydro-9-oxa-10-phosphaphenanthrene-10-oxide (DOPO) and 100 mL of dioxane (AR) into a 250ml four-necked bottle, and blow nitrogen Stir and heat up to 90°C, after DOPO is completely dissolved, start to drop 13g of HOCH 2 CF 2 O(CF 2 CF 2 O) 13 (CF 2 O) 10 CF 2 CH 2OH perfluoropolyether diol (ZDOL) with stirring, the ZDOL dropping speed is 0.5mL / min, and the stirring speed is 300r / min. After the dropwise addition is completed, the temperature is raised to 80°C, and the reactant is rotated for 1 hour to recover the dioxygen. Hexacyclic, a viscous product was obtained after the reaction, and then washed 5 times with absolute ethanol, and vacuum-dried at 70°C for 10 hours to obtain the modified flame retardant DOPO-ZDOL.
[0032] Step 2. In a 500ml three-necked flask, add 250mL of acetone solution of H302 hydroxy...
Embodiment 3
[0037] 1. Preparation of flame-retardant modified fluorine-containing hyperbranched polyurethane-epoxy acrylate resin copolymer:
[0038] Step 1. Add 25g of H302 hydroxyl-terminated hyperbranched polyester (purchased from Wuhan Hyperbranched Resin Technology Co., Ltd.) (DOPO) and 150 mL of dioxane (AR) into a 250mL four-necked bottle, blow in nitrogen and stir to raise the temperature to 90°C, after DOPO is completely dissolved, start to drop 20g of HOCH 2 CF 2 O(CF 2 CF 2 O) 10 (CF 2 O) 12 CF 2 CH 2 OH perfluoropolyether diol (ZDOL) with stirring, the ZDOL dropping speed is 0.8mL / min, and the stirring speed is 400r / min. After the dropwise addition is completed, the temperature is raised to 85°C, and the reactant is rotated for 1 hour to recover the dioxygen. Six rings, a viscous product was obtained after the reaction, and then washed with absolute ethanol for 5 times, and vacuum-dried at 60°C for 10 hours to obtain the modified flame retardant DOPO-ZDOL.
[0039] S...
PUM
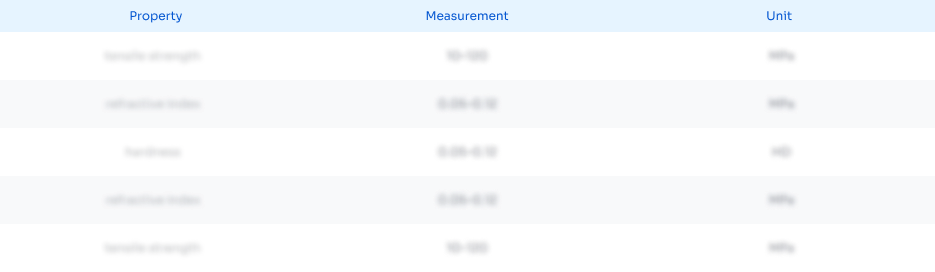
Abstract
Description
Claims
Application Information

- R&D
- Intellectual Property
- Life Sciences
- Materials
- Tech Scout
- Unparalleled Data Quality
- Higher Quality Content
- 60% Fewer Hallucinations
Browse by: Latest US Patents, China's latest patents, Technical Efficacy Thesaurus, Application Domain, Technology Topic, Popular Technical Reports.
© 2025 PatSnap. All rights reserved.Legal|Privacy policy|Modern Slavery Act Transparency Statement|Sitemap|About US| Contact US: help@patsnap.com