Online detection and control system for fusion depth in additive manufacturing process
An additive manufacturing and control system technology, applied in manufacturing tools, measuring devices, auxiliary welding equipment, etc., can solve problems such as difficult high-temperature weld detection, no weld penetration system, and intelligent manufacturing difficulties.
- Summary
- Abstract
- Description
- Claims
- Application Information
AI Technical Summary
Problems solved by technology
Method used
Image
Examples
Embodiment Construction
[0011] In order to make the object, technical solution and advantages of the present invention clearer, the present invention will be further described in detail below in conjunction with the accompanying drawings and embodiments. It should be understood that the specific embodiments described here are only used to explain the present invention, not to limit the present invention.
[0012] The present invention provides an online penetration detection and control system for additive manufacturing, including: a processing module 1, a welding component 2, an infrared image acquisition device 3, a wireless transceiver component 4, and a pose adjustment component 5; the welding component 2 includes a welding controller 21. Welding equipment 22; the wireless transceiver component 4 includes a wireless transmitter 41 and a wireless receiver 42; the pose adjustment component 5 includes a pose controller 51, an electric push rod 52, and an angle adjustment mechanism 53; the processing ...
PUM
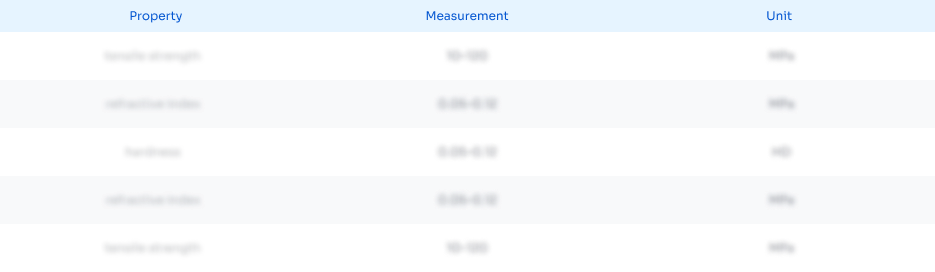
Abstract
Description
Claims
Application Information

- R&D
- Intellectual Property
- Life Sciences
- Materials
- Tech Scout
- Unparalleled Data Quality
- Higher Quality Content
- 60% Fewer Hallucinations
Browse by: Latest US Patents, China's latest patents, Technical Efficacy Thesaurus, Application Domain, Technology Topic, Popular Technical Reports.
© 2025 PatSnap. All rights reserved.Legal|Privacy policy|Modern Slavery Act Transparency Statement|Sitemap|About US| Contact US: help@patsnap.com