Turbocharger bearing body structure with integral ball bearing
A technology of turbocharger and bearing body, applied in machine/engine, engine components, mechanical equipment, etc., can solve problems such as high reliability requirements and poor working conditions of ball bearings, and achieve reduced wear, simple structure, and sufficient lubrication. Effect
- Summary
- Abstract
- Description
- Claims
- Application Information
AI Technical Summary
Problems solved by technology
Method used
Image
Examples
Embodiment 1
[0023] Such as Figure 1-4 As shown, the turbocharger bearing body structure with integral ball bearing includes bearing body 1, integral ball bearing, positioning pin 3 and oil inlet bolt 4.
[0024] The bearing body 1 is provided with an axial bearing hole 11, and the outer wall of the bearing body 1 is provided with a radial stepped hole. A section of the stepped hole close to the bearing hole 11 of the bearing body 1 is a pin hole A122;
[0025] The integral ball bearing is installed in the bearing hole 11 of the bearing body 1 . The integral ball bearing includes an outer ring 21, an inner ring 22, a ceramic ball rolling body 23 and a cage 24. The outer ring 21 is provided with a pin hole B and a lubricating oil supply hole 212, and the lubricating oil supply hole 212 and the bearing body 1 enter oil. The oil outlet port 131 of the hole 13 is connected. There are two rows of ceramic ball rolling elements 23, and the two rows of ceramic ball rolling elements 23 are respe...
PUM
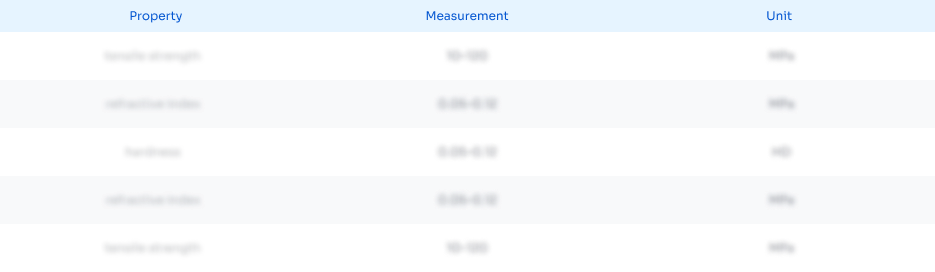
Abstract
Description
Claims
Application Information

- R&D
- Intellectual Property
- Life Sciences
- Materials
- Tech Scout
- Unparalleled Data Quality
- Higher Quality Content
- 60% Fewer Hallucinations
Browse by: Latest US Patents, China's latest patents, Technical Efficacy Thesaurus, Application Domain, Technology Topic, Popular Technical Reports.
© 2025 PatSnap. All rights reserved.Legal|Privacy policy|Modern Slavery Act Transparency Statement|Sitemap|About US| Contact US: help@patsnap.com