Heating mixer for board raw materials
A heat mixer and raw material technology, applied in the field of plate processing, can solve the problems of low work efficiency, high energy consumption, poor mixing effect, etc., and achieve the effects of simple structure, energy saving and work efficiency improvement
- Summary
- Abstract
- Description
- Claims
- Application Information
AI Technical Summary
Problems solved by technology
Method used
Image
Examples
Embodiment
[0018] like figure 1 As shown, a heat mixer for sheet materials includes a barrel 1, a feed port 2, a discharge port 3, a rotating shaft 4, a rotating motor 5, and a plurality of stirring shafts 6, and the barrel 1 is arranged horizontally; The feed inlet 2 is arranged on the top of the barrel 1, and the outlet 3 is arranged on the bottom of the barrel 1; the rotating shaft 4 is arranged through the barrel 1 and is located at the central axis of the barrel 1; The rotating motor 5 is arranged on the left end of the barrel 1 and is connected with the left end of the rotating shaft 4; the rotating shaft 4 is provided with a friction roller 7, and the axis of the rotating shaft 4 of the friction roller 7 is consistent; The plurality of agitating shafts 6 are arranged in the barrel 1, pass through the friction drum 7 and are evenly distributed in the circumferential direction of the rotating shaft 4; Specifically, the barrel 1 is fixed by a frame 9 .
[0019] Specifically, a plur...
PUM
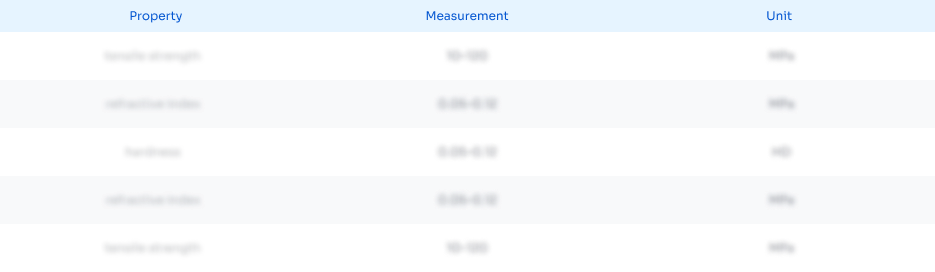
Abstract
Description
Claims
Application Information

- Generate Ideas
- Intellectual Property
- Life Sciences
- Materials
- Tech Scout
- Unparalleled Data Quality
- Higher Quality Content
- 60% Fewer Hallucinations
Browse by: Latest US Patents, China's latest patents, Technical Efficacy Thesaurus, Application Domain, Technology Topic, Popular Technical Reports.
© 2025 PatSnap. All rights reserved.Legal|Privacy policy|Modern Slavery Act Transparency Statement|Sitemap|About US| Contact US: help@patsnap.com