Claus tail-gas processing technology
A Claus tail gas and treatment process technology, which is applied in the field of Claus tail gas treatment process, can solve the problems of increased energy consumption and achieve the effects of simplified construction, energy saving and guaranteed desulfurization effect
- Summary
- Abstract
- Description
- Claims
- Application Information
AI Technical Summary
Problems solved by technology
Method used
Image
Examples
Embodiment Construction
[0030] The specific embodiment of the present invention will be further described below in conjunction with accompanying drawing:
[0031] like figure 1 Shown, a kind of Claus tail gas treatment technique described in the present invention comprises the steps:
[0032] 1) The Claus tail gas from the Claus process sulfur condenser is mixed with the reducing gas and enters the hydrogenation reactor 2 after exchanging heat with the process gas from the first-stage reactor in the first-stage process gas heat exchanger 1 , convert almost all of the sulfur and sulfides in the Claus tail gas into H 2 S;
[0033] 2) The Claus tail gas coming out from the hydrogenation reactor 2 enters the second-stage process gas heat exchanger 3 to exchange heat with the process gas entering the second-stage reactor for cooling, and then passes through the three-pass sulfur condenser 4 to produce low-pressure steam, from which After the Claus tail gas from the three-pass sulfur condenser 4 is cool...
PUM
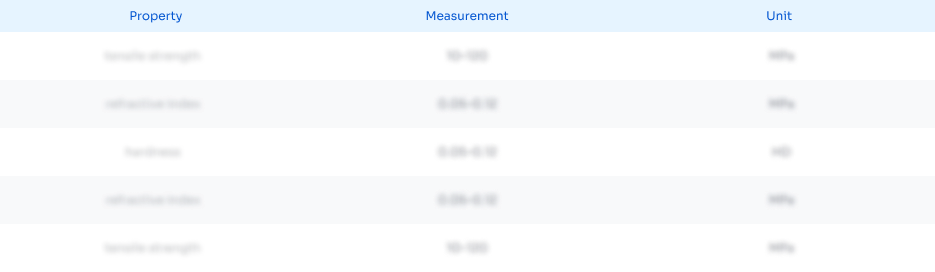
Abstract
Description
Claims
Application Information

- R&D Engineer
- R&D Manager
- IP Professional
- Industry Leading Data Capabilities
- Powerful AI technology
- Patent DNA Extraction
Browse by: Latest US Patents, China's latest patents, Technical Efficacy Thesaurus, Application Domain, Technology Topic, Popular Technical Reports.
© 2024 PatSnap. All rights reserved.Legal|Privacy policy|Modern Slavery Act Transparency Statement|Sitemap|About US| Contact US: help@patsnap.com