Motion compensation detection device for robot terminal
A motion compensation and detection device technology, applied in measurement devices, instruments, manipulators, etc., can solve the problems of lack of error repair and compensation ability, low efficiency, execution errors, etc., to improve flexibility and accuracy, flexible and convenient use, and detection. high precision effect
- Summary
- Abstract
- Description
- Claims
- Application Information
AI Technical Summary
Problems solved by technology
Method used
Image
Examples
Embodiment Construction
[0015] In order to make the technical means, creative features, goals and effects achieved by the present invention easy to understand, the present invention will be further described below in conjunction with specific embodiments.
[0016] like figure 1 The robot terminal motion compensation detection device includes a bearing base 1, a guide rail 2, a slider 3, a transparent protective cover 4, a displacement sensor 5, a pressure sensor 6, a distance measuring device 7, a height measuring device 8, The width measuring device 9, the 3D camera 10 and the data processing circuit 11, the guide rail 2 are installed on the outer surface of the robot terminal equipment 12 and distributed parallel to the axis of the robot terminal equipment 12, and the bearing base 1 passes through the slider 3 and the guide rail 2 Sliding connection, each guide rail 2 is equipped with a bearing base 1, displacement sensor 5, pressure sensor 6, distance measuring device 7, height measuring device 8,...
PUM
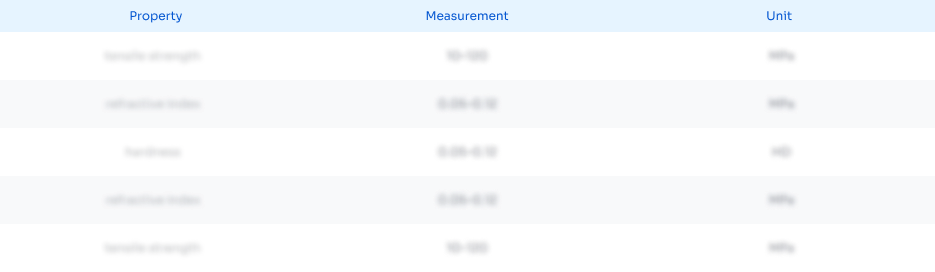
Abstract
Description
Claims
Application Information

- R&D Engineer
- R&D Manager
- IP Professional
- Industry Leading Data Capabilities
- Powerful AI technology
- Patent DNA Extraction
Browse by: Latest US Patents, China's latest patents, Technical Efficacy Thesaurus, Application Domain, Technology Topic, Popular Technical Reports.
© 2024 PatSnap. All rights reserved.Legal|Privacy policy|Modern Slavery Act Transparency Statement|Sitemap|About US| Contact US: help@patsnap.com