Fine particle embedded cassiterite beneficiation method
A beneficiation method and fine particle technology, which are applied in chemical instruments and methods, flotation, wet separation, etc., can solve the problems of poor rationality and high flotation cost, achieve stable beneficiation, improve the efficiency of shaking table gravity separation, and improve separation efficiency. Efficient effect
- Summary
- Abstract
- Description
- Claims
- Application Information
AI Technical Summary
Problems solved by technology
Method used
Image
Examples
Embodiment 1
[0033] Such as figure 1 Shown, this fine-grained cassiterite beneficiation method, its specific steps are as follows:
[0034] (1) Fine-grained cassiterite ore (the raw ore tin grade of a tin mine in Myanmar is 0.55wt%, and the main mineral composition is cassiterite, pyrite, quartz, calcite, etc.) Grinding to -0.074 by rod mill mm accounts for 85%, adjust the pulp until the pulp concentration is 25wt%, and add 150g of copper sulfate and 2000g of oxalic acid as regulator, 200g of butyl xanthate as collector, and 20g of terpineol as foaming agent on the basis of per ton of ore , carry out a pre-desulfurization flotation roughing to obtain sulfur rough concentrate and sulfur roughing tailings;
[0035] (2) Slurry the crude sulfur concentrate obtained in step (1) until the pulp concentration is 25wt%, and perform blank concentration, the number of separations can be 1, and the selected tailings are returned to the upper level of flotation in order to obtain sulfur Concentrate; ...
Embodiment 2
[0046] Such as figure 1 Shown, this fine-grained cassiterite beneficiation method, its specific steps are as follows:
[0047] (1) Fine-grained cassiterite ore (the raw ore tin grade of a tin mine in Myanmar is 0.6wt%, and the main mineral composition is cassiterite, pyrite, quartz, calcite, etc.) Grinding to -0.074 by rod mill mm accounts for 80%, adjust the pulp until the pulp concentration is 25wt%, and add 150g of copper sulfate and 2000g of oxalic acid as regulator, 200g of butyl xanthate as collector, and 20g of terpineol as foaming agent on the basis of per ton of ore , carry out a pre-desulfurization flotation roughing to obtain sulfur rough concentrate and sulfur roughing tailings;
[0048] (2) Slurry the crude sulfur concentrate obtained in step (1) until the pulp concentration is 25wt%, and perform blank concentration, the number of separations can be 1, and the selected tailings are returned to the upper level of flotation in order to obtain sulfur Concentrate; ...
Embodiment 3
[0059] Such as figure 1 Shown, this fine-grained cassiterite beneficiation method, its specific steps are as follows:
[0060] (1) Fine-grained cassiterite ore (the raw ore tin grade of a tin mine in Myanmar is 0.5wt%, and the main mineral composition is cassiterite, pyrite, quartz, calcite, etc.) Grinding by rod mill to -0.074 mm accounts for 85%, adjust the pulp until the pulp concentration is 25wt%, and add 150g of copper sulfate and 2000g of oxalic acid as regulator, 200g of butyl xanthate as collector, and 20g of terpineol as foaming agent on the basis of per ton of ore , carry out a pre-desulfurization flotation roughing to obtain sulfur rough concentrate and sulfur roughing tailings;
[0061] (2) Slurry the crude sulfur concentrate obtained in step (1) until the pulp concentration is 25wt%, and perform blank concentration, the number of separations can be 1, and the selected tailings are returned to the upper level of flotation in order to obtain sulfur Concentrate; ...
PUM
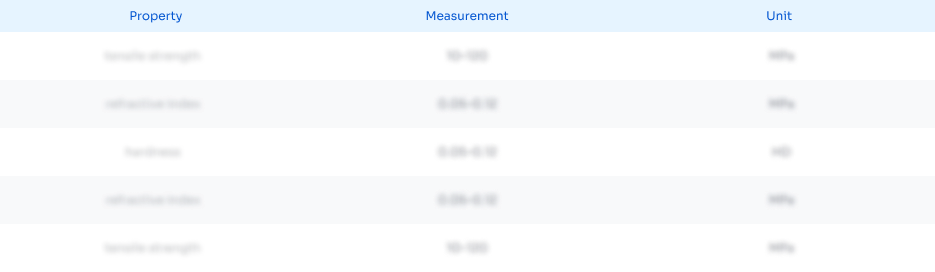
Abstract
Description
Claims
Application Information

- R&D
- Intellectual Property
- Life Sciences
- Materials
- Tech Scout
- Unparalleled Data Quality
- Higher Quality Content
- 60% Fewer Hallucinations
Browse by: Latest US Patents, China's latest patents, Technical Efficacy Thesaurus, Application Domain, Technology Topic, Popular Technical Reports.
© 2025 PatSnap. All rights reserved.Legal|Privacy policy|Modern Slavery Act Transparency Statement|Sitemap|About US| Contact US: help@patsnap.com