Method for achieving plasticity parameter parametric inversion recognition of welding nuclear area material
A technology of plastic parameters and regions, applied in the direction of analyzing materials, testing the hardness of materials, and testing the strength of materials by applying stable tension/pressure. The effect of improving efficiency
- Summary
- Abstract
- Description
- Claims
- Application Information
AI Technical Summary
Problems solved by technology
Method used
Image
Examples
Embodiment Construction
[0035] Such as figure 1 As shown, this embodiment includes the following steps:
[0036] Step 1, design the sample and carry out the Vickers hardness test: the test material selected in this embodiment is 304l stainless steel, and the designed hardness sample is as follows figure 2shown. In the hardness test, the variation range of the test load is 0.025-0.5kgf, four tests are carried out under each load and the diagonal length of the obtained indentation is measured. The relationship between the load and the diagonal length is shown in Table 1:
[0037] Table 1 304l stainless steel force-diagonal length measurement results
[0038]
[0039] Step 2. Convert the diagonal length of the indentation into the indentation depth: convert the diagonal length value in Table 1 into the indentation depth, and the obtained force-depth relationship data is shown in Table 2:
[0040] Table 2 304l stainless steel force-depth relationship data
[0041]
[0042] image 3 To draw th...
PUM
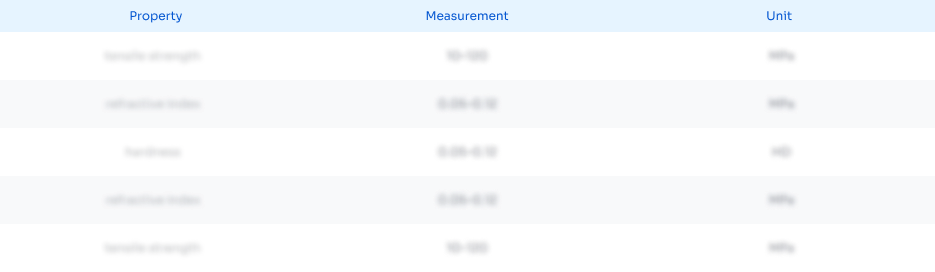
Abstract
Description
Claims
Application Information

- R&D
- Intellectual Property
- Life Sciences
- Materials
- Tech Scout
- Unparalleled Data Quality
- Higher Quality Content
- 60% Fewer Hallucinations
Browse by: Latest US Patents, China's latest patents, Technical Efficacy Thesaurus, Application Domain, Technology Topic, Popular Technical Reports.
© 2025 PatSnap. All rights reserved.Legal|Privacy policy|Modern Slavery Act Transparency Statement|Sitemap|About US| Contact US: help@patsnap.com