High-precision star sensor installation matrix in-orbit real-time calibration method
A technology for installing matrix and star sensors, which is applied in the field of on-orbit real-time calibration of high-precision star sensor installation matrix, can solve the problems that the fusion results cannot meet the requirements, and solve the problems of filter performance degradation or even divergence, avoiding failure and avoiding errors Effect
- Summary
- Abstract
- Description
- Claims
- Application Information
AI Technical Summary
Problems solved by technology
Method used
Image
Examples
Embodiment Construction
[0064] According to Figure 1 ~ Figure 6 , A detailed description of the preferred embodiments of the present invention.
[0065] Considering that the structure of the star sensor is affected by the space thermal environment during its orbit operation, the structure is deformed. The present invention is based on the quaternion adaptive Kalman filter principle (hereinafter referred to as q-AKF), and adjusts the current shooting position in real time according to the measurement residual The weight in the filtering avoids the problem of degraded filtering performance or even divergence due to inaccurate models.
[0066] Such as figure 1 As shown, the present invention provides an on-orbit real-time calibration method for a high-precision star sensor installation matrix, which includes the following steps:
[0067] Step S1: Calculate the quaternion of the actual installation relationship;
[0068] Step S2: Perform filter calibration on the vector part of the installation relationship q...
PUM
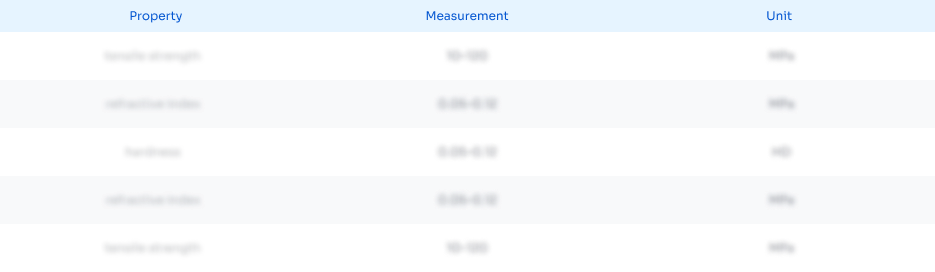
Abstract
Description
Claims
Application Information

- R&D
- Intellectual Property
- Life Sciences
- Materials
- Tech Scout
- Unparalleled Data Quality
- Higher Quality Content
- 60% Fewer Hallucinations
Browse by: Latest US Patents, China's latest patents, Technical Efficacy Thesaurus, Application Domain, Technology Topic, Popular Technical Reports.
© 2025 PatSnap. All rights reserved.Legal|Privacy policy|Modern Slavery Act Transparency Statement|Sitemap|About US| Contact US: help@patsnap.com