Spherical wire walking robot and walking method thereof
A robot, spherical technology, applied in the direction of manipulators, motor vehicles, manufacturing tools, etc., can solve the problems of limiting mechanism adjustment ability, large space, limited swing range and swing speed of the rotating rod, etc., to achieve compact structure, small mechanism size, adaptability strong effect
- Summary
- Abstract
- Description
- Claims
- Application Information
AI Technical Summary
Problems solved by technology
Method used
Image
Examples
Embodiment Construction
[0031] The technical solutions of the present invention will be further described below in conjunction with the embodiments shown in the accompanying drawings.
[0032] The spherical wire walking robot of the present invention has a structure comprising an outer spherical shell 1, a middle spherical shell 2 and an inner spherical shell 3 concentric with the center of the sphere, the inner spherical shell 3 has a larger moment of inertia as an inertial rotor, and the outer spherical shell 1 is placed in the horizontal ring frame 5, and the tops of the left and right hemispherical shells of the outer spherical shell 1 are respectively provided with horizontal left and right roller shafts 6, and the left and right roller shafts 6 are respectively installed on the ring frame 5 through bearing structures Above, the bearing structure is provided with an encoder that detects the rotation parameters of the ring frame 5 relative to the outer spherical shell 1; a semicircular groove 4 ( ...
PUM
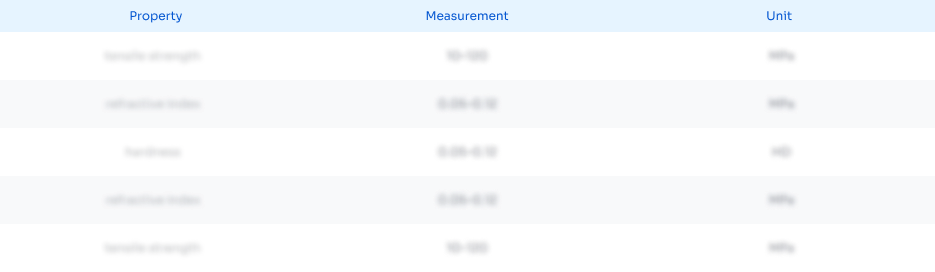
Abstract
Description
Claims
Application Information

- R&D Engineer
- R&D Manager
- IP Professional
- Industry Leading Data Capabilities
- Powerful AI technology
- Patent DNA Extraction
Browse by: Latest US Patents, China's latest patents, Technical Efficacy Thesaurus, Application Domain, Technology Topic, Popular Technical Reports.
© 2024 PatSnap. All rights reserved.Legal|Privacy policy|Modern Slavery Act Transparency Statement|Sitemap|About US| Contact US: help@patsnap.com