Multiscale Numerical Simulation Method for Drilling of Carbon Fiber Reinforced Composite Materials
A technology of reinforced composite materials and numerical simulation, applied in the field of mechanical processing, can solve the problems of low precision and efficiency, and achieve the effect of high precision and fast speed
- Summary
- Abstract
- Description
- Claims
- Application Information
AI Technical Summary
Problems solved by technology
Method used
Image
Examples
Embodiment Construction
[0028] Below in conjunction with example the present invention is further described.
[0029] A multi-scale numerical simulation method for drilling carbon fiber reinforced composite materials, which includes the following steps:
[0030] First, the meso-constitutive and macro-constitutive modeling of the matrix and fibers is carried out. Take T700 carbon fiber reinforced composite single-layer unidirectional (0°) plate as an example. Through experiments, its longitudinal tensile ultimate strength is 1830.7MPa, longitudinal ultimate compressive strength is 895.16MPa, transverse tensile limit is 31.31MPa, transverse compressive limit is 124.54MPa, longitudinal Young's modulus is 99.22GPa, and transverse Young's modulus is 7.05GPa. The material is divided into infinitely small stress units, and the tensile (compressive) ultimate stress in the X, Y, and Z directions and the ultimate shear stress in the XY, XZ, and YZ planes are calculated according to the classical material mech...
PUM
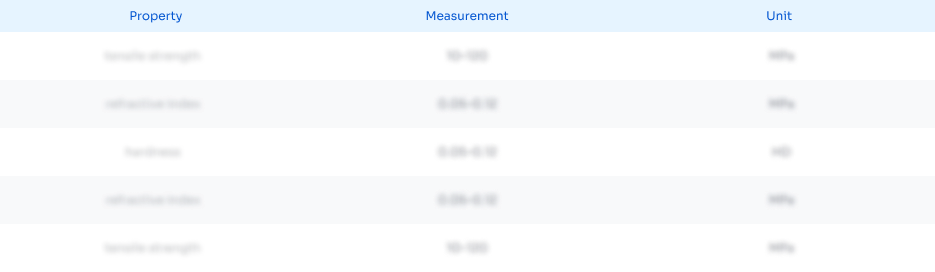
Abstract
Description
Claims
Application Information

- R&D
- Intellectual Property
- Life Sciences
- Materials
- Tech Scout
- Unparalleled Data Quality
- Higher Quality Content
- 60% Fewer Hallucinations
Browse by: Latest US Patents, China's latest patents, Technical Efficacy Thesaurus, Application Domain, Technology Topic, Popular Technical Reports.
© 2025 PatSnap. All rights reserved.Legal|Privacy policy|Modern Slavery Act Transparency Statement|Sitemap|About US| Contact US: help@patsnap.com