Machine tool spindle conical hole coping device
A technology for machine tool spindles and taper holes, which is applied in the direction of grinding drive devices, grinding machine parts, and machine tools designed for grinding the rotating surface of workpieces. Achieve the effect of solving downtime for repair and reducing the cost of maintenance points
- Summary
- Abstract
- Description
- Claims
- Application Information
AI Technical Summary
Problems solved by technology
Method used
Image
Examples
Embodiment Construction
[0018] Preferred embodiments of the present invention will now be described in detail, and the preferred embodiments of the present invention will be specifically described below with reference to the accompanying drawings.
[0019] A machine tool spindle taper hole grinding device, comprising a horizontally laid bottom plate E, on which a grinding part and an adjusting device for adjusting the position of the grinding part are arranged, and the adjusting device includes a The vertical driving part that moves vertically and the horizontal driving part that drives the grinding part to move horizontally;
[0020] The grinding part includes a rod-shaped grinding head C, the top of the grinding head C extends vertically upwards, the bottom end of the grinding head C is fixed on the output shaft of the grinding head motor D through a clamp K, and the output shaft of the grinding head motor D is connected to the Grinding head C coaxial;
[0021] The vertical drive part includes a v...
PUM
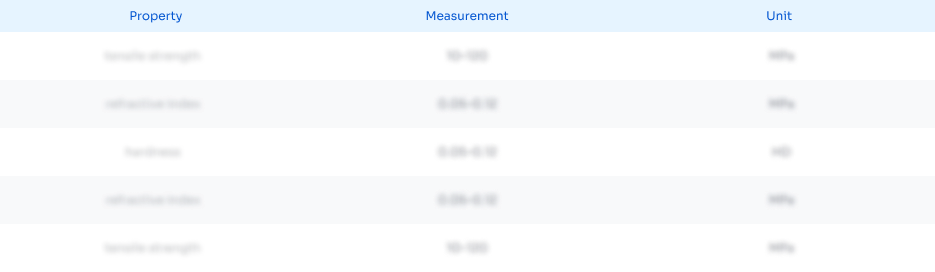
Abstract
Description
Claims
Application Information

- R&D
- Intellectual Property
- Life Sciences
- Materials
- Tech Scout
- Unparalleled Data Quality
- Higher Quality Content
- 60% Fewer Hallucinations
Browse by: Latest US Patents, China's latest patents, Technical Efficacy Thesaurus, Application Domain, Technology Topic, Popular Technical Reports.
© 2025 PatSnap. All rights reserved.Legal|Privacy policy|Modern Slavery Act Transparency Statement|Sitemap|About US| Contact US: help@patsnap.com