Heavy-duty locomotive multistage idling fault detection method
A technology for fault detection and heavy-duty locomotives, applied in instruments, simulators, control/regulation systems, etc., and can solve problems such as single influencing factor and slow calculation speed
- Summary
- Abstract
- Description
- Claims
- Application Information
AI Technical Summary
Problems solved by technology
Method used
Image
Examples
Embodiment 1
[0088] Such as figure 1 As shown, according to the adhesive characteristic curve, there is dμ / dv on the left side of the peak point, that is, the stable region s >0, on the right side of the peak point, that is, there is dμ / dv in the idle zone s s The symbol of the locomotive makes it difficult to obtain the running status of the locomotive; the following formula, The notation for is not equivalent to Therefore, although μ characterizes the situation of wheel-rail surface adhesion utilization, it cannot utilize To identify the running condition of the wheelset.
[0089]
[0090] According to the change of traction and the speed of locomotive body is unknown, the methods of locomotive idling detection are discussed respectively.
[0091] (1)T m change, the traction force of the locomotive changes at this time,
[0092] a. which is As the output torque of the locomotive increases, the creep speed increases and the adhesion coefficient increases, indicating that t...
Embodiment 2
[0106] Combined with the simulation experiment, the application effect of the present invention is described in detail.
[0107] Aiming at the detection of multi-stage idling faults of wheel sets, a single-axis machine simulation model is established by Matlab / Simulink for verification.
[0108] Simulation 1, such as image 3 As shown, the initial value of the input torque is 0, and then increases in the range of 2000N·m / s, from Figure 4 It can be seen that the coefficient of adhesion increases before 4.2s and decreases after 4.2s. Figure 6 As shown in the judgment diagram, 1 is idling and 0 is stable. At 4.2s, when switching from 0 to 1, the locomotive is idling microscopically, and then the locomotive is idling slowly, and the adhesion coefficient decreases. and Figure 5 The angular acceleration judgment diagram also shows that the car has been idling rapidly at 4.3s.
[0109] Simulation 2, such as Figure 7 The input torque is shown, the initial value is 8000N·m, and...
PUM
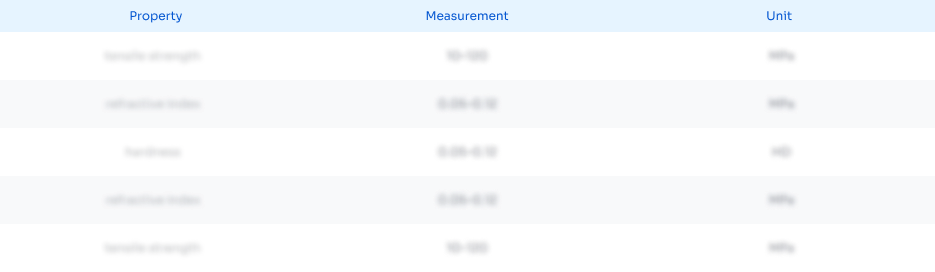
Abstract
Description
Claims
Application Information

- R&D
- Intellectual Property
- Life Sciences
- Materials
- Tech Scout
- Unparalleled Data Quality
- Higher Quality Content
- 60% Fewer Hallucinations
Browse by: Latest US Patents, China's latest patents, Technical Efficacy Thesaurus, Application Domain, Technology Topic, Popular Technical Reports.
© 2025 PatSnap. All rights reserved.Legal|Privacy policy|Modern Slavery Act Transparency Statement|Sitemap|About US| Contact US: help@patsnap.com