Forming method for shell of airplane cover
A molding method and machine cover technology, applied in the field of carbon fiber products, can solve the problems of unqualified finished product performance, affecting the uniformity of product density, and difficulty in laying carbon fiber cloth evenly and evenly, so as to ensure the performance of finished products, uniform distribution of glue injection points, The effect of ensuring uniformity
- Summary
- Abstract
- Description
- Claims
- Application Information
AI Technical Summary
Problems solved by technology
Method used
Image
Examples
Embodiment Construction
[0026] The present invention will be described in further detail below in conjunction with the accompanying drawings and specific embodiments.
[0027] Depend on Figure 1 to Figure 6 As can be seen from the structural representation of the molding die used in the molding method of the aircraft cover shell of the present invention shown, it comprises the following steps:
[0028] 1) Make a special forming mold, the forming mold includes an upper mold 3, a lower mold 2 and an inclined roof mechanism, the upper mold and the lower mold form a product cavity after the mold is closed, and the forming slider 4 and the upper core of the product cavity are formed. The inserts 5 can be detachably connected to the lower mold 2, the inclined top mechanism is set in the upper mold 3, and the inclined top slider 7 is located on the surface of the cavity; the forming mold is provided with seven injection holes connected with the product cavity. point 6, and the seven glue injection points ...
PUM
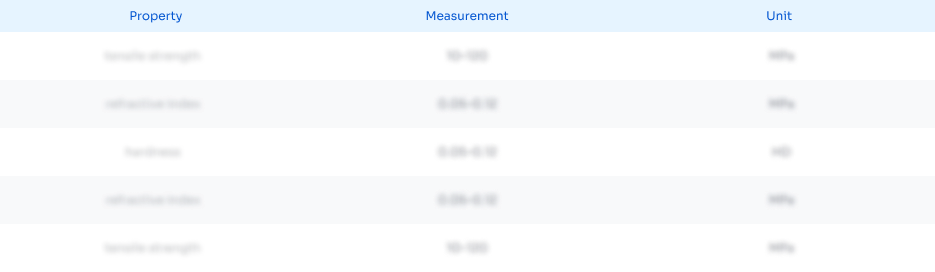
Abstract
Description
Claims
Application Information

- R&D
- Intellectual Property
- Life Sciences
- Materials
- Tech Scout
- Unparalleled Data Quality
- Higher Quality Content
- 60% Fewer Hallucinations
Browse by: Latest US Patents, China's latest patents, Technical Efficacy Thesaurus, Application Domain, Technology Topic, Popular Technical Reports.
© 2025 PatSnap. All rights reserved.Legal|Privacy policy|Modern Slavery Act Transparency Statement|Sitemap|About US| Contact US: help@patsnap.com