Composite facing material
A composite paste and matrix layer technology, applied in the field of materials, can solve the problems of non-wear resistance, abrasion, neglect of wear resistance, impact resistance, waterproof performance, etc., to ensure softness, solve the problems of non-impact resistance, non-wear resistance, Effect of improving impact and wear resistance
- Summary
- Abstract
- Description
- Claims
- Application Information
AI Technical Summary
Problems solved by technology
Method used
Examples
Embodiment 1
[0020] A composite veneer material, which sequentially includes a wear-resistant layer, a matrix layer and an adhesive layer from top to bottom, the wear-resistant layer and the matrix layer are co-extruded, and the matrix layer is bonded to the adhesive layer with hot melt adhesive;
[0021] The wear-resistant layer is made of the following components in mass percentage:
[0022] EPDM: 40%,
[0023] PP: 56%,
[0024] Peroxide DCP: 1%,
[0025] Cross-linking modifier multifunctional epoxy resin: 3%;
[0026] The base layer is formed by adding foaming agent and crosslinking agent DCP microfoaming 10 times by POE;
[0027] The adhesive layer is fabric.
Embodiment 2
[0029] A composite veneer material, which sequentially includes a wear-resistant layer, a matrix layer and an adhesive layer from top to bottom, the wear-resistant layer and the matrix layer are co-extruded, and the matrix layer is bonded to the adhesive layer with hot melt adhesive;
[0030] The wear-resistant layer is made of the following components in mass percentage:
[0031] EPDM: 70%,
[0032] PP: 26%,
[0033] Peroxide DCP: 3%,
[0034] Cross-linking modifier multifunctional epoxy resin: 1%;
[0035] The base layer is formed by adding foaming agent and cross-linking agent DCP micro-foamed 20 times by POE;
[0036] The adhesive layer is fabric.
Embodiment 3
[0038] A composite veneer material, which sequentially includes a wear-resistant layer, a matrix layer and an adhesive layer from top to bottom, the wear-resistant layer and the matrix layer are co-extruded, and the matrix layer is bonded to the adhesive layer with hot melt adhesive;
[0039] The wear-resistant layer is made of the following components in mass percentage:
[0040] EPDM: 50%,
[0041] PP: 25%,
[0042] Peroxide DCP: 2.5%,
[0043] Cross-linking modifier multifunctional epoxy resin: 2.5%;
[0044] The base layer is formed by adding foaming agent and cross-linking agent DCP micro-foaming 15 times from POE;
[0045] The adhesive layer is fabric.
PUM
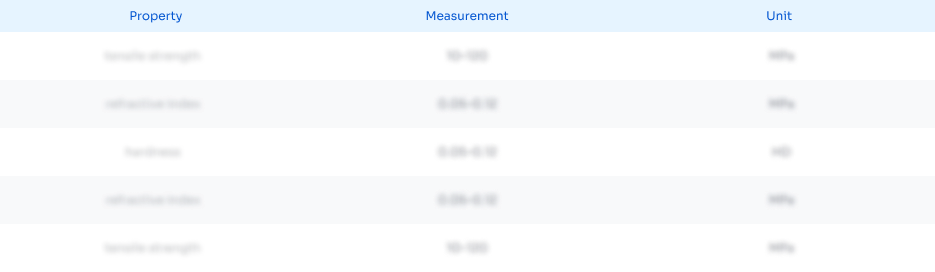
Abstract
Description
Claims
Application Information

- R&D
- Intellectual Property
- Life Sciences
- Materials
- Tech Scout
- Unparalleled Data Quality
- Higher Quality Content
- 60% Fewer Hallucinations
Browse by: Latest US Patents, China's latest patents, Technical Efficacy Thesaurus, Application Domain, Technology Topic, Popular Technical Reports.
© 2025 PatSnap. All rights reserved.Legal|Privacy policy|Modern Slavery Act Transparency Statement|Sitemap|About US| Contact US: help@patsnap.com