Part recognizing and sorting method and system based on machine vision
A machine vision and sorting system technology, applied in the field of parts identification, can solve the problems of small imaging area of parts, imaging interference, missed shots of small parts, etc. The effect of difficulty and high functional integration
- Summary
- Abstract
- Description
- Claims
- Application Information
AI Technical Summary
Problems solved by technology
Method used
Image
Examples
Embodiment Construction
[0033] Below in conjunction with accompanying drawing and specific embodiment the present invention will be described in further detail:
[0034] The machine vision-based parts recognition and sorting method shown in the figure includes the following steps:
[0035] S1 Collect sample parts images, perform feature extraction on sample parts images and build parts template library;
[0036] S2 Judging whether the component to be detected has reached the detection area, and judging the attributes of the component, including size, magnetism and non-magneticity;
[0037] S3 Image acquisition and feature extraction of the parts to be tested: large parts directly perform image acquisition and feature extraction; small magnetic parts are sucked by a magnetic chuck for image acquisition and feature extraction; non-magnetic small parts are sucked by a vacuum chuck and then Carry out image acquisition and feature extraction; among them, the image acquisition is realized by a manipulator...
PUM
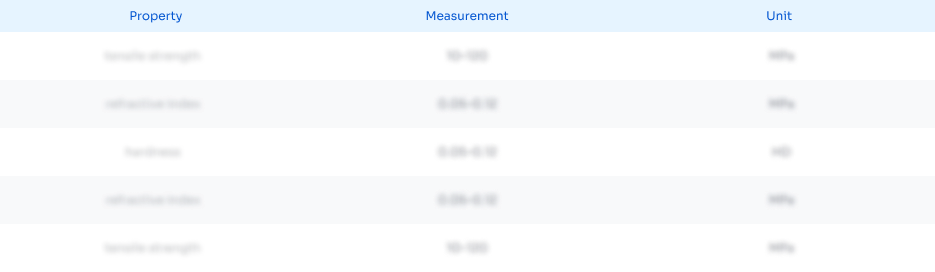
Abstract
Description
Claims
Application Information

- R&D Engineer
- R&D Manager
- IP Professional
- Industry Leading Data Capabilities
- Powerful AI technology
- Patent DNA Extraction
Browse by: Latest US Patents, China's latest patents, Technical Efficacy Thesaurus, Application Domain, Technology Topic, Popular Technical Reports.
© 2024 PatSnap. All rights reserved.Legal|Privacy policy|Modern Slavery Act Transparency Statement|Sitemap|About US| Contact US: help@patsnap.com